Технология производства ДСП (древесностружечных плит). Технология производства дсп
Технология производства ДСП (древесностружечных плит)
Древесностружечные плиты за последние 10—15 лет стали, очевидно, одним из самых известных и распространенных древесных материалов. Они являются основным конструкционным материалом в производстве мебели, а в последнее время получают все большее признание и в строительстве, в частности в производстве малоэтажных домов.
Сырье для древесностружечных плит — различного вида отходы лесопиления, лесозаготовок, деревообработки (горбыли, рейки, откомлевки, сучья, срезки, стружка, опилки), а также низкокачественные круглые лесоматериалы. Становится понятным значимость этого производства: из отходов и низкокачественной древесины получается материал, из которого изготовляют высококачественные, долговечные изделия.
Все кусковые отходы измельчаются в щепу на рубительных машинах. Из щепы, а также из стружки, отходов и опилок на специальных роторных станках приготовляется стружка. Из круглых лесоматериалов стружка изготовляется или непосредственно из бревна на станках с ножевым валом, или по схеме щепа — стружка, когда сначала изготовляется щепа, а затем из щепы стружка. Перед подачей бревен на струженный станок их разрезают на мерные заготовки (обычно длиной 1 м).
Стружка должна иметь определенные, наперед заданные размеры (толщина 0,2—0,5 мм, ширина 1 — 10 мм, длина 5—40 мм). В наружные слои плиты направляется стружка наименьших размеров. Кроме соблюдения размеров необходимо также следить, чтобы стружка была плоской, равномерной толщины, с ровной поверхностью. Стружка для наружных слоев после стружечных станков проходит дополнительное измельчение на дробилках (здесь уменьшается ширина) или в мельницах, где изменяется толщина. Последняя операция имеет особое значение для плит, которые отделываются методом ламинирования, так как в этом случае предъявляются высокие требования к качеству их поверхности.
Изготовленная сырая стружка хранится в бункерах, куда подается системой пневмотранспорта или механическими транспортерами. Из бункеров сырая стружка подается в сушилки. Сушить стружку необходимо до влажности 4—6%, а для внутреннего слоя — до 2—4%. Поэтому стружку разных слоев сушат в отдельных сушилках. В производстве древесностружечных плит используются, как правило, конвективные сушилки, в большинстве случаев барабанного типа. В топке сушилки сжигается газ или мазут, температура в ней 900— 1000° С. На входе в барабан Температура сушильного агента достигает 450—550° С, на выходе она от 90 до 120° С. Барабан имеет диаметр 2,2 м и длину 10 м, устанавливается он с наклоном в 2—3° в сторону входа сырой стружки.
После сушки стружка сортируется или на механических (ситовых) агрегатах, или пневматически. На этих машинах происходит разделение стружки на фракции для наружных и внутренних слоев. На этом заканчивается изготовление стружки. Автор должен заметить, что эта часть технологического процесса во многом предопределяет успешное выполнение последующих операций, производительность процесса и особенно качество плит. Поэтому приготовлению стружки (работе оборудования на этом участке, квалификации операторов) уделяется большое внимание.
Стружка смешивается со связующим в специальных агрегатах, Называемых смесителями. Операция эта сложная, поскольку технология производства требует покрытия связующим каждой стружки. Неосмоленные стружки не склеиваются, а излишняя смола на стружке приводит к перерасходу связующего и плохому качеству плит. Связующее в смеситель подается в виде растворов. Их концентрация в потоке наружного слоя 53— 55%, внутреннего слоя несколько больше (60—61%). В настоящее время наиболее распространены смесители, в которых распыленное связующее (размеры частиц 30—100 мкм) факелом направляется на поток взвешенных в воздухе стружек. Эти два потока перемешиваются, связующее осаждается на поверхности стружек. Смесители, как правило, нуждаются в тонком регулировании, при котором соблюдаются строгие количественные соотношения между стружкой, смолой и отвердителем. После осмоления стружка ленточными или скребковыми транспортерами направляется в формирующие машины.
Формирующие машины принимают осмоленную стружку и высыпают ее ровным слоем (ковром) на проходящие под ними поддоны или ленточные транспортеры. Стружечный ковер — это непрерывная лента определенной ширины и толщины. Он разделяется на пакеты, из которых и образуются в последующем при горячем прессовании плиты. Естественно, что равномерность насыпки ковра прямым образом влияет на качество плит (равноплотность, равнотолщинность). Кроме того, формирующие машины должны насыпать во внешние слои мелкие стружки.
Конвейер перемещает пакеты, которые после прохождения пресса для подпрессовки становятся плотными, обладающими транспортной прочностью брикетами. В настоящее время в промышленности древесностружечных плит известно два принципиально различных типа главных конвейеров. Они различаются тем, что в одном случае пакеты (а затем брикеты) перемещаются на металлических поддонах, в другом типе главного конвейера — на ленточных транспортерах, когда прессование бесподдонное. Каждая схема главного конвейера имеет преимущества и недостатки. Поддонный способ более простой и надежный, но плиты получаются с большей разнотолщинностью, расход тепловой энергии больше. Бесподдонный способ обеспечивает некоторую экономию энергии, повышенное качество плит. Конструкции главных конвейеров достаточно подробно описаны в специальной литературе, и при необходимости читатель может с -ее помощью более детально изучить эту основную технологическую линию заводов древесностружечных плит.
Автор уже упоминал, что в состав главного конвейера входит пресс для подпрессовки. Подпрессовка необходима для уменьшения толщины пакета и повышения его транспортабельности. Толщина пакета уменьшается в 2,5—4 раза (больше при бесподдонном прессовании). Давление при этом составляет 1—1,5 МПа при прессовании на поддонах и 3—4 МПа при бесподдонном прессовании. Подпрессовка производится обычно в одноэтажных прессах, иногда это бывает подвижный пресс, чаще — стационарный.
После подпрессовки брикеты на поддонах поступают в многоэтажный гидравлический пресс для горячего прессования. При бесподдонном прессовании брикеты выкладываются лентой непосредственно на горячие плиты пресса; При прессовании на брикет воздействуют тепло и давление. Читателю, очевидно, понятно, что продолжительность горячего прессования предопределяет продолжительность цикла работы пресса и тем самым производительность всего завода. Поэтому уделяется большое внимание уменьшению цикла прессования. Стоимость пресса для горячего прессования, как и в производстве древесноволокнистых плит, составляет 20— 25% стоимости всего оборудования завода, и поэтому проблема его лучшего использования — постоянная забота работников заводов, а профессия оператора пресса — самая почитаемая.
Прессование производится при 180°С и удельном давлении 2,5—3,5 МПа. Продолжительность прессования 0,3—0,35 мин на 1 мм толщины плиты. Современные прессы имеют размеры горячих плит, достигающие 6x3 м, до 22 рабочих промежутков (одновременно прессуются 22 древесностружечные плиты). Высота пресса достигает 8 м.
Сокращение цикла прессования (увеличение производительности пресса) достигается за счет повышения температуры прессования, применения смол с меньшей продолжительностью отверждения, увеличения количества рабочих промежутков. Эти мероприятия реализованы на большинстве заводов, что позволило поднять производительность прессов с 35 до 80—85 тыс. м3 плит в год.
Автор считает необходимым информировать читателя о том, что имеются и одноэтажные прессы. У них длина горячих плит достигает 20 м, а общая длина главного конвейера —60—70 м. При его обслуживании оператор для перемещения вынужден использовать велосипед.
Готовые плиты пресса выгружаются на приемную (разгрузочную) этажерку, а с нее на линию, где они обрезаются с четырех сторон (линию форматной обрезки). В состав этой линии часто входит агрегат для охлаждения плит. Затем они укладываются в стопы, где выдерживаются не менее 5 суток. Далее плиты шлифуются на оборудований и инструментом, которые были описаны выше. В соответствии с требованиями стандарта плиты сортируются, а затем или раскраиваются на заготовки для мебельных щитов, или отправляются потребителям полноформатными.
В заключение укажем, что на 1 м3 древесностружечных плит расходуется 1,75—1,85 м3 древесины, 70— 80 кг смолы (в пересчете на сухое вещество), 1,4— 1,5 т пара, 160—170 кВт-ч электроэнергии. Затраты труда составляют 2,5—4 чел.-ч на 1 м3.
Необходимо отметить, что производство древесностружечных плит непрерывно совершенствуется: появляются новые виды плит, принципиально новые машины, более эффективные связующие. Представляют, в частности, интерес плиты из стружки, размеры которых по длине и ширине составляют десятки миллиметров; стружка располагается в плоскости плиты. Это обеспечивает высокую прочность плит на статический изгиб, что важно при их применении в строительстве. Такие плиты (из ориентированной крупноформатной стружки) с успехом заменяют фанеру, которая становится все более дефицитной.
В последние годы стали использовать нетоксичные быстроотверждающиеся смолы, что увеличивает производительность прессов, а значит, и заводов, ликвидирует загазованность в цехах, позволяет использовать плиты внутри жилых помещений. Объем производства древесностружечных плит непрерывно растет, эта тенденция сохранится и в будущем. Для отрасли, оснащенной современным оборудованием, нужны высококвалифицированные рабочие, инженеры и техники, хорошо знающие технологию и механической и химической переработки древесины, электронику, гидравлику, теплотехнику.
www.stroitelstvo-new.ru
Технология производства дсп: слова главного технолога
Здравствуйте уважаемые читатели блога, на связи Андрей Ноак. Сегодня я расскажу как выглядит технология производства дсп. Кстати часть чертежей я делал самолично, извините за хвастовство *pardon* , но очень хочется позвездится *rofl* ! А делал я эти чертежи когда защищал диплом по производству древесностружечных плит на бывшем заводе КИСК или КрасПлитПром, что в городе Красноярск. Далее я выполнял две пуско наладки заводов по изготовлению древесностружечной плиты и поэтому могу вам более чем подробно рассазать о изготовлении этих плит.
Моя новая книга
Хочу начать с хорошей новости, недавно вышла моя новая книга, более подробно о ней можно узнать в разделе «МОИ КНИГИ». Информация которая в книге — это настоящая информационная бомба, такого в России пока нет!
Книга «Технология изготовления ДСП от А до Я» основана на личном опыте и опыте работы немецких специалистов. Более подробно о книжечке в разделе «КНИГИ».
Периодически я провожу вебинары по деревообработке, на которых обсуждаются самые интересные и актуальные вопросы деревообработки. Следите за новыми статьями и узнаете когда будет следующий вебинар.
Также у меня можно заказать индивидуальную консультацию по деревообработке. Я как никто знаю какие ошибки делают производители оборудования, так как у меня есть опыт. К примеру строят завод на 200 тыс в год плиты и не учитывают диаметр входящего сырья, а я вот знаю что надо это учитывать! Более подробно о консультациях в разделе «УСЛУГИ».
Технология изготовления дсп
Изготовление плиты начинается с подачи круглого сырья краном на раскатный стол, далее лес распиливатся на чураки длиной около одного метра. Вы не поверите, но эта уникальная технология с чураками используется только на линиях с торцовочными станками! Из этих самых чураков в стружечных станках с ножевым валом получали сырье отличного качества.
Но в связи с лишней операцией торцовки леса, развитие изготовления пошло по другой технологии. Эта технология сегодня более распространена, здесь получают щепу с производительных дробилок с ножевым валом или диском, а затем уже щепу перерабатывают на центробежных стружечных станках в нужную фракцию.

Организация склада хранения и подачи древесного сырья в производстве дсп.
Полученную фракцию подают в сушильное отделение и затем происходит сортировка стружки еще по фракциям. Отсортированная по слоям стружка осмоляется, насыпается формашиной в непрерывный ковер и прессуется. Полученная плита шлифуется и укладывается в пакеты.
Изготовление дсп очень сложное. Сложное в плане технологии, поясню почему. Для того чтобы иметь хорошую отдачу от производства, необходимо иметь очень квалифицированные кадры, так как на одном и том же оборудовании при одной и той же схеме можно делать совсем разные объемы производства и совсем разное качество.
Причем под квалифицированными кадрами я понимал не операторский состав, а именно инженерно технических работников способных обучить рабочих работать.
При грамотной работе инженерной службы, оператору за хорошую зарплату нужно будет только вовремя явиться на работу, нажать кнопку на запуск оборудования, убрать рабочее место (а если все отстроено, так и убирать нечего будет), и не забыть выключить кнопку в конце рабочего смены. А обеспечить именно такую работу оборудования должны инженеры.
Производство ДСтП очень зависит от грамотного и квалифицированного управления. Итак ее изготовление состоит из следующих операций:
- Первый вариант получение из круглой древесины чураков. Второй вариант получение щепы от поставщиков или из привезенной древесины путем дробления.
- Получение из чураков нужной фракции, второй вариант получение из щепы стружки на стружечных станках.
- Сушка.
- Трехходовой сушильный барабан, именно он работает на одной из самых распространенных и опасных технологий по сушке...

Сортировка стружки — один из важных этапов технологии производства плиты.
- Смешивание сухих опилок наружного и внутреннего слоя с заданным количеством связующего (смола, отвердитель, добавки) для каждого слоя, в смесителях.

Расходомеры электромагнитные, для измерения объемов подаваемой смолы... Самое современное оборудование на данный момент...
- Насыпка ковра с нижним, средним и верхним слоями формашиной.
- Подпрессовка и при необходимости разделение ковра
- Горячее прессование ковра по заданной циклограме и при соответствующей настройке пресса.
- Обрезка кромок, охлаждение и кондиционирование плиты.
- Складирование не шлифованной плиты. В некоторых типах оборудования данная операция отсутствует. На рисунке ниже нарисована линия с прессом непрерывного прессования. А вообще имеется несколько типов линий по производству ДСтП с своими достоинствами и недостатками, читайте это на нашем блоге в более ранних статьях.

Оптимизированный участок хранения древесной плиты.
- Шлифование и раскрой плиты в размер с своими нюансами.
- Сортировка готовой плиты по ГОСТ. Кстати большинство производителей сейчас делает свое ТУ. В ТУ увеличиваются или уменьшаются допуски, может увеличиваться количество сортов. Но это должна быть временная норма, так как для получения максимальной прибыли должно идти 99% первого сорта.
Конечно это только одна из технологий ДСтП, в зависимости от типов линий, она может значительно меняться.
Тематическое видео, как делается дсп в домашних условиях из бамбука:
Для того чтобы выбрать оптимальную технологию производства плиты, нужно прочитать огромный объем литературы, пообщаться с профессионалами знающими многие тонкости в работе оборудования и работавшими на этом оборудовании, потому что каждый тип оборудования по производству древесностружечной плиты имеет свои плюсы и минусы в работе.
До новых встреч и читайте мой блог чтобы быть в курсе всех новинок в деревообработке!
andreynoak.ru
Производство ДСП: технология и оборудование
Производство ДСП – это выгодное дело. Материал пользуется значительной популярностью у современных мастеров. Это не только удобный и экологичный, но и простой в обработке материал. Он представляет собой листовой композитный элемент, в основе изготовления которого лежит методика опрессовывания горячих отходов деревообрабатывающего производства. Во многих случаях предполагается введение в состав массы дополнительных добавок.
Сфера применения ДСП
Сегодня древесно-стружечные плиты нашли весьма широкое применение на практике. Преимущественно их используют в рамках мебельного производства и при изготовлении дверей. Еще плиты актуальны для строительной отрасли, при выполнении отделочных работ, в сфере автомобилестроения и многих других современных производствах.
Отлаженное производство ДСП способно принести значительную прибыль. На начальном этапе его организации требуется найти доступное сырье по приемлемой цене. Сложностей с реализацией готовой продукции не возникнет.
Способы производства
Процесс производства ДСП сводится к обработке посредством горячего прессования деревообрабатывающих отходов, предварительно подготовленных. В составе рабочей массы, помимо стружечной смести, присутствует и термореактивная смола с клеящими свойствами.
Исходным сырьем для будущих плит бывают щепки и опилки, а также прочие отходы бумажного и деревообрабатывающего производства. Достаточно смешать их со специальной смолой и уложить в форму. Там в условиях горячего пресса и температурного воздействия, смола проявит свои клеящие свойства.
Завершающим этапом технологического процесса является охлаждение готовых древесно-стружечных плит и их отделение от форм. Далее, их отправляют на шлифовку.

Схема производства ДСП
Необходимое оборудование
В производстве ДСП требуются определенные машины и агрегаты. Технологический процесс не обходится без следующего оборудования:

Оборудование для производства ДСП
- смесители;
- формовочные агрегаты;
- горячий пресс;
- охладители;
- устройства для выравнивания боковин;
- шлифовальные машины.
Изначально в смесителях соединяются все компоненты для рабочей массы с учетом рекомендованных объемов. Дальнейшая напрессовка бумаги осуществляется уже агрегатами для формовки исходной смеси, в горячих прессах.
Указанный перечень является минимально необходимым для изготовления ДСП. Он касается производств, когда в работу поступает предварительно подготовленное сырье.
Когда процесс производства ДСП осуществляется с применением обычного сырья, возникнет необходимость в установке еще некоторых агрегатов. Обычно это строгальные и рубильные машины, мельницы или оборудование для раскройки.
Нередко руководители производства предпочитают дополнительно укомплектовать его дополнительными машинами, что позволяет значительно увеличить его эффективность и технологичность. В таких случаях устанавливаются агрегаты для вентиляции, транспортеры различного типа, вибросита, сушильные камеры, штабелеры и многое другое.
Стоимость готовой производственной линии
Итоговая стоимость комплекта оборудования для изготовления ДСП зависит от его производительности и некоторых других факторов. При небольшом выходе в пределах сотни готовых листов в день, придется вложить до 200 тыс. евро. Чем выше производительность – тем дороже обойдется комплект.
Еще один определяющий фактор цены на такое оборудование – это его изготовитель. Большинство отдают предпочтение продукции проверенных европейских брендов, но она всегда будет стоить на порядок дороже, нежели китайские аналоги.

Линия по производству ДСП
При составлении бизнес-плана по производству ДСП в больших объемах, измеряющихся тысячами кубических метров готовых изделий, необходимо предусмотреть расходы на:
- производственное оборудование соответствующей мощности и производительности;
- вспомогательные машины и агрегаты;
- установку приобретенного оборудования и его наладку;
- подготовку помещения с достаточной площадью, соответствующее действующим требованиям и санитарным производственным нормам для изготовления ДСП.
Процесс изготовления ДСП
Получают древесно-стружечные плиты с применением горячего пресса. В первоначальное сырье добавляется смола, обладающая специальными клеящими свойствами и некоторые другие добавки. Подготовленная масса разливается по формам, где в дальнейшем протекает процесс склеивания под воздействием внешних условий.
Основные этапы в процессе изготовления ДСП:
- подготовительный этап;
- формовка;
- прессование;
- обработка в соответствии с требуемыми размерами;
- шлифовка.
На начальном этапе в специализированных машинах смешиваются исходные составляющие рабочей смеси – деревообрабатывающие отходы и смола наряду с отвердителями и иными необходимыми компонентами. Важно строго соблюдать рекомендованные пропорции составляющих, чтобы готовый материал получил желаемые свойства.
Готовая масса подвергается формовке и опрессовке. Манипуляции осуществляются при воздействии высокой температуры.
Завершается технологический процесс удалением излишков с готовых листов посредством их обрезки с последующей шлифовкой на специальном оборудовании.
От правильности исполнения каждого из основных этапов процесса производства древесно-стружечных плит будет зависеть их конечное качество.
Ламинированное ДСП

Схема ламинирования ДСП
ЛДСП, более известный в качестве ламинированного ДСП, представляет собой стандартные древесно-стружечные плиты.
Единственное их отличие от традиционных листов состоит в том, что каждый лист имеет дополнительное покрытие. Этот ламинат несет преимущественно декоративную нагрузку.
В качестве ламината применяется специализированная пленка.
Преимущественно материал ЛДСП актуален для мебельных производств. А также его используют и в других отраслях современной промышленности.
Наряду с внешней красотой, указанный материал характеризуется некоторыми минусами. Не получится разделить готовую плиту на меньшие части в домашних условиях без применения специализированного оборудования. Ламинирующий слой легко откалывается, что делает края изделия неаккуратными.

Ламинированное ДСП
Сам процесс ламинирования – это специальная отделка готовых изделий. Операция предполагает дополнительный технологический этап в рамках производственного процесса – напрессовку специального покрытия. Эта пленка закрепляется по холодной либо по горячей методике. В первом случае нагрева поверхностей не предполагается. При обращении к горячей методике ламинирующий слой закрепляется посредством клеящих свойств смолы в исходной массе.
Эта поверхность не предполагает дальнейших отделочных манипуляций.
Изготовление древесно-стружечных плит – это нужный, прибыльный и перспективный процесс при верной его первоначальной организации. Данный продукт всегда востребован на рынке строительных материалов.
Видео: Производство ДСП
promzn.ru
Оборудование + Технология как делают плиты в 2018
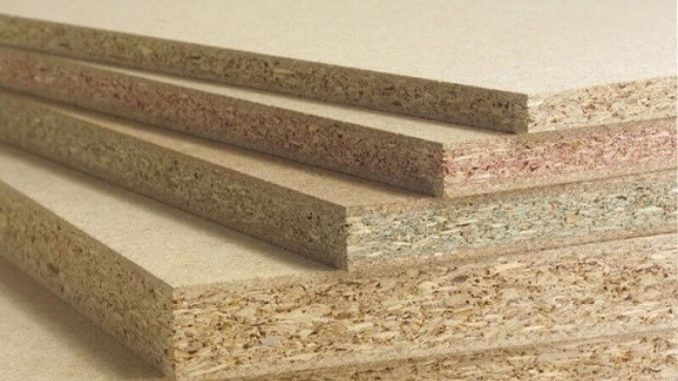
Древесно-стружечная плита (ДСтП, ДСП) — это листовой композиционный материал, производимый путём горячего прессования древесных частиц, преимущественно стружки, смешанных со связующим веществом неминерального происхождения с введением при необходимости специальных добавок (6-18 % от массы стружек) на одно- и многоэтажных периодических прессах 0,2-5 МПа, 120-190 °С) или в непрерывных ленточных, гусеничных либо экструзионных агрегатах.
Технология и оборудование для производства ДСП
В качестве основного сырья для производства ДСП используют отходы лесопильной промышленности. Кусковые отходы для производства измельчают до щепы на специальных рубильных машинах. Из стружки, опилок, отходов и щепы делают стружку на специальных роторных станках. Что касается круглого лесоматериала, то стружка делается из бревна на специальных станках, которые имеют ножевые валы. Перед тем как подают бревно на стружечный станок, его разрезают на мерные заготовки, длина которых составляет один метр. Сама же стружка должна иметь определенные размеры, а именно: ширина должна быть от одного до десяти миллиметров, длина составлять от пяти до сорока миллиметров, и толщина составлять от 0,2 до 0,5 миллиметров. На наружный слой плиты ДСП направляют стружку меньших размеров. Помимо соблюдения размеров, также необходимо следить за тем, чтобы она имела плоскую форму, которая должна соответствовать ровной поверхности и равномерной толщины. Для наружных слоев стружка после стружечного станка должна проходить дополнительное измельчение на специальных дробилках. Или же проходить в мельницах, где необходимо изменить толщину.
Производство ДСП на последней операции имеет особое значение для изготовления плит, которые отделывают ламинированным способом. Именно в этом процессе предъявляются самые высокие требования, как к поверхности, так и к качеству. Готовая сырая стружка надежно хранится в специальных бункерах. В эти бункеры подается механический транспортер и система пневмотранспорта. После этого ее направляют в сушилку, где необходимо просушить ее до четырех или шести процентов влажности. Что касается внешнего слоя, то он должен составлять от двух до четырех процентов. Что касается производства ДСП с разными слоями, то для каждого слоя осуществляется отдельная сушка. На производстве применяют по правилам только конвективные сушилки, но чаше всего отправляют на барабанное оборудование.
В сушилке можно подвергать сжиганию, как мазут, так и газ, так как температура в таком оборудовании составляет 1000 градусов по Цельсию. На входе в барабан, температура сушильного агента должна составлять 550 градусов по Цельсию, а на выходе до 120 градусов по Цельсию. Сам барабан имеет длину десяти метров, а диаметр составляет 2,2 метра.
После того как она будет полностью высушена, ее подвергают сортировке на специальных механических агрегатах, или же машинах пневматического действия. Производство ДСП на таких машинах осуществляется быстро, надежно и качественно. На таких машинах осуществляется разделение стружки на определенные фракции, как для внутреннего, так и наружного слоя. На этом этапе заканчивается производство стружки.
Готовую стружку необходимо смешать со связующими в специальном агрегате, который называют смесителем. Такая операция считается самой сложной, так как производственная технология будет требовать от процесса покрытие каждой стружки. Если стружки для ДСП будут не осмоленные, то их невозможно будет склеить, при этом будет оставаться лишняя смола, которая приведет к перерасходам и плохому качеству будущих плит. Что касается связующих, то их подают в виде раствора, так как их концентрация в наружном слое составляет 55 процентов, а во внутреннем слое составляет 61 процент. Сегодня самым распространенным смесителем, в котором применяют распыленные связующие считают факелом, который направляет поток взвешенных стружек для производства ДСП в воздух.
За счет такого потока, в процессе перемешки, связывающие оседают на поверхность стружки. Смесители должны тонко регулироваться и соблюдать строгие соотношения количества между смолой, отвердителем и стружкой. После того как стружку осмолили с помощью скребкового или ленточного транспортера, ее направляют в формирующую машину. Где такая машина должна высыпать стружку ровным слоем на проходящий поддон или транспортер. Само понятие стружечный ковер имеет вид непрерывной ленты, которая должна определять толщину и ширину. Ковер разделятся на пакеты, из которых образуются в последующем плиты при горячем прессовании.
Видео как делают ДСП:
Здесь нужно учитывать то, что равномерная насыпка ковра будет влиять на качество плиты ДСП, а именно на толщину и на плотность. Помимо этого, формирующие машины должны в обязательном порядке насыпать мелкую стружку во внешний слой.
Читайте также
moybiznes.org
Производство ДСП (древесностружечных плит)
Древесностружечные плиты (ДСП) являются новым материалом не только в СССР, но и за рубежом. Организация производства дсп за рубежом началась после второй империалистической войны в связи с острым дефицитом лесных материалов, необходимостью более полно использовать заготавливаемую древесину и отходы лесопильно-деревообрабатывающего производства, а также широким развитием химии, обеспечившей это производство необходимыми синтетическими клеями.
Рост производства древесностружечных плит за 1950—1965 гг. характеризуется данными, приведенными в табл. 3.
В СССР производство ДСП (древесностружечных плит) впервые было организовано в 1956 г. на ряде мебельных предприятий. Мощность таких цехов была незначительна и не превышала 3—5 тыс. м3 в год.
Таблица 3. Производство древесностружечных плит в тыс. тСтраны | 1962 г. | 1963 г. | 1964 г. | 1965 г. |
Всего в мире | 2900 | 3500 | 4500 | 4800 |
Европа | 1906 | 2476 | 3025 | 3349 |
США | 473 | 574 | 665 | 730 |
Канада | 43 | 57 | 65 | 75 |
Швеция | 70 | 82 | 90 | 100 |
Норвегия | 80 | 90 | 95 | 110 |
Финляндия | 77 | 78 | 91 | 130 |
Франция | 220 | 286 | 340 | 400 |
Польша | — | 56 | 73 | 82 |
ФРГ | 673 | 731 | 880 | 940 |
СССР | 430 | 530 | 592 | 798 |
За весьма короткий срок в СССР была создана новая отрасль промышленности мощностью около 650 тыс. м3 в год. Кроме тот, в стадии завершения строительства находится 60 цехов общей проектной мощностью 1724 тыс. м3.
К 1970 г. объем производства ДСП должен быть доведен до 3500 тыс. м3 в год, из которых 1000 тыс. м3 будут применены в строительстве.
Несмотря на достигнутые успехи, производство древесностружечных плит на душу населения в СССР отстает от США и Финляндии более чем в 2 раза (США —0,18 кг, СССР —0,08 кг).
Основными задачами, стоящими перед промышленностью древесностружечных плит, являются улучшение технологии производства, повышение качества и удешевление себестоимости изготовляемых плит.
В соответствии с ГОСТ 10632—63 ДСП изготовляются следующих марок: ПС-1— плоского прессования, среднего веса, однослойные; ПТ-1—плоского прессования тяжелые однослойные; ПС-3 — плоского прессования среднего веса трехслойные; ПТ-3 — плоского прессования, тяжелые трехслойные; ЭСС — экструзионные среднего веса сплошные; ЭТС — экструзионные тяжелые сплошные; ЭЛМ — экструзионные легкие многопустотные.
Размеры плит: длина — 1520, 2000, 2500 и 3500 мм; ширина — 1250, 1500 и 1750 мм, толщина — 10, 13, 16, 19, 22, 25, 30, 35, 40 и 50 мм.
Физико-механические свойства древесностружечных плит должны соответствовать требованиям, приведенным в табл. 4.
При производстве плит из древесных частиц сырье подвергается дроблению, но не до степени волокна, как это имеет место при производстве древесноволокнистых плит. Размер и форма древесных частиц, а также способ их изготовления в значительной степени влияют на качество готовых плит. Существенное влияние оказывает также качество и количество смол, применяемых для склейки частиц.
Плиты изготовляют прессованием или штампованием с вытяжкой: при этом древесные частицы в плитах располагаются различным образом, что в свою очередь сказывается на качестве, свойствах и применении плит.
Таблица 4. Физико-механические свойства древесностружечных плит (ГОСТ 10632—63)Марка плиты | Группа плиты | Объемный вес в г/см3 | Предел прочности в кгс/см2, не менее | Разбухание по толщине в %, не более | ||
при статическом изгибе | при растяжении перпендикулярно пласти плита | с гидрофобными добавками | без гидрофобных добавок | |||
ПС-1, ПС-3 | А/Б | 0,5—0,65 | 170/130 | 3 | 14 | 22 |
ПТ-1, ПТ-3 | А/Б | 0,66—0,8 | 215/170 | 3,5 | 18 | 25 |
ЭСС | А/Б | 0,5—0,65 | 100/80 | Не нормируется | ||
ЭТС | А/Б | 0,66—0,8 | 120/100 | |||
ЭЛМ | А/Б | 0,35—0,5 | 60/40 |
Использование плит из древесных частиц весьма разнообразно, однако при применении их следует учитывать, что при изготовлении плит пользуются двумя принципиально различными способами прессования. Плиты, прессованные в пластинчатом прессе, имеют структуру, при которой частицы расположены параллельно поверхности плиты. К этому виду плит относятся однослойные и многослойные плиты со специальной или другого рода высококачественной облицовкой. В штампованных с вытяжкой плитах древесные частицы расположены перпендикулярно поверхности плиты. Эта разница в расположении частиц обусловливает совершенно различные качества плит в трех основных направлениях: по длине, ширине и толщине.
В плитах, штампованных с вытяжкой, усадка и разбухание по толщине минимальны, но значительны в других направлениях. Такие плиты недостаточно прочны на изгиб и, как правило, должны быть облицованы каким-нибудь другим материалом (фанерой, шпоном, пластиком, бумагой и др.). Следует отметить, что метод изготовления плит штампованием с вытяжкой позволяет выпускать плиты с отверстиями, что невозможно сделать при других методах производства.
Изготовление плит с отверстиями снижает их объемный вес до 0,6—0,7 г/м3. Отверстия могут занимать до 30% площади поперечного сечения плиты.
Теплопроводность любого вида плит из древесных частиц изменяется в зависимости от их плотности. Чем плотнее плита, тем выше коэффициент теплопроводности. Для пустотелых плит коэффициент теплопроводности определяют экспериментально.
Сопротивление выдергиванию гвоздей и винтов или поперечное сопротивление у плит из древесных частиц ниже, чем у древесины всех пород той же плотности. Поэтому крепление плит осуществляют специально сконструированными для этой цели соединениями. Огнестойкость и сопротивление гниению и повреждению термитами у плит из древесных частиц выше, чем у древесины или другого применяемого для изготовления плит лигноцеллюлозного материала.
Для еще большего повышения огнестойкости плиты подвергают специальной обработке или покрывают жаростойкими красками. Плиты из древесных частиц, применяемые в местах, где велика опасность гниения или повреждения термитами, для придания им стойкости против таких повреждений подвергают специальной обработке.
Прочность изоляционных плит ниже, чем у плит более высокой плотности, поэтому эти плиты используют в качестве полуфабриката для среднего слоя в мебельном производстве, для столярных работ и изготовления дверей или же для внутренней облицовки зданий и др.
Практика использования изоляционных древесностружечных плит еще невелика.
Плиты средней плотности применяют в качестве облицовочного материала там, где необходимы незначительная прочность и жесткость конструкции. В основном их используют для внутренней отделки помещений, устройства полов (как прокладка под линолеум) и устройства опалубки. Самое широкое применение плиты находят в производстве бытовой, кухонной и встроенной мебели, при этом изготавливаемую из древесных частиц плиту облицовывают фанерой или пластическими материалами, а углы и края панелей часто обкладывают натуральной древесиной. Плиты хорошо обрабатываются обычными деревообрабатывающими ручными и электрифицированными инструментами.
Твердые плиты, так же как и полутвердые, применяют для изготовления мебели и в строительстве. Кроме того, из твердых плит можно изготовлять крышки верстаков, модельных плит для литейного производства и др.
www.stroitelstvo-new.ru
китайские и немецкие, выбираем лучшие
Здравствуйте уважаемые читатели Блога Андрея Ноака. Сегодня я опишу существующие типы линий по производству ДСП, а также их достоинства и недостатки которыми обладает каждая линия дсп. Также будет рассказано небольшое количество нюансов, которые, если их учесть, при грамотном монтаже оборудования будут очень облегчать работу и соответственно снижать себестоимость готовой продукции. Итак начнем, хотя сначала я расскажу о своей новой книге которая может быть вам полезна...
Мои услуги и литература
Постоянно я выпускаю новую и актуальную литературу по деревообработке. В ней дана просто убойная информация о современных технологиях и способах работы на плитных производствах. Книга основана на личном опыте и опыте работы немецких специалистов. Более подробно о книжечке в разделе «КНИГИ».
Периодически я провожу вебинары по деревообработке, на которых обсуждаются самые интересные и актуальные вопросы деревообработки. Следите за новыми статьями и узнаете когда будет следующий вебинар.
Также у меня можно заказать индивидуальную консультацию по деревообработке. Я как никто знаю какие ошибки делают производители оборудования, так как у меня есть опыт. К примеру строят завод на 200 тыс в год плиты и не учитывают диаметр входящего сырья, а я вот знаю что надо это учитывать! Более подробно о консультациях в разделе «УСЛУГИ».
Ах, да еще хочу сказать про еще одну книжку, она рассказывается о технологии изготовления 3D древесностружечных плит. В России пока такие плиты никто не выпускает, поэтому вы можете быть первыми! Аналогов книги в России и странах СНГ нет. Более подробно о ней в разделе «МОИ КНИГИ».
Разновидности оборудования для ДСП
Производство дсп осуществляется на нескольких разновидностях линий, при этом каждая может иметь как преимущества так и недостатки. Основной критерий по которому определяется принадлежность линии это конструкция пресса. Существуют следующие виды прессов:
- Одноэтажный пресс.
- Многоэтажный пресс.
- Каландровый пресс для дсп.
- Непрерывный пресс.
1) Самые продвинутые это непрерывные пресса, их производительность 300-500 тыс. кубов в год, на них можно держать припуск на шлифование до 0.8мм, меньше уже не рекомендуют в связи с плохим приклеиванием ламината на плиту. Особым плюсом является возможность варьировать конечные размеры готовых плиты после таких прессов.
Современные такого типа разделены на две части. Первая часть это высокотемпературная, где происходит непосредственное прессование плиты. Вторая часть служит для охлаждения плиты, температура на данном участке снижается.
Данная инновация позволяет получать существенное снижение брака по причине получения пузырей и разрыва плиты. Обязательной особенностью является наличие подпрессовщика в конвейере.
2) Одноэтажный пресс, его преимущество в том что можно держать при прессовании высокую температуру, для его монтажа фундамент меньше делается чем для многоэтажного пресса. Одноэтажный пресс имеет достаточно большой размер плит, длина более 12 метров, ширина от 2 метров.
Размер это их преимущество по сравнению с многоэтажными прессами, допустим на многоэтажных прессах можно на плите держать одну ширину и длину, на одноэтажных можно менять длину плиты (преимущество перед конкурентами). Припуск на шлифование на этих прессах доводят до 1 мм.
Производительность этих линий зависит от объема одной запрессовки, если запрессовка около 0.5м3, то производительность будет около 50000. Производительность оборудования периодического действия как правило зависит от объема одной запрессовки, и количество листов производимых за смену.
Производительность можно расчитать как отношение времени работы смены 11 часов к времени одной запрессовки от 3 до 8 минут, умноженное на объем одной запрессовки.
Если хорошо и долго поработать на прессе то цикл прессования можно сделать менее 3 минут, все зависит от технолога. К недостатку некоторых одноэтажных прессов отнесу транспортировочную стальную ленту, очень слабое место оборудования, и я писал свой отзыв о работе такого оборудования.
3) Многоэтажный пресс. Оборудование с данными прессами подразделяются на поддонные и бес поддонные. Поддонное прессование совсем уже устарело, здесь прессование осуществляется на алюминиевых или сеточных поддонах, поддоны быстро изнашиваются, плита идет с большой разнотолщинностью до 2 мм.
Бес поддонное пресование более современное, но разнотолщинность тоже большая около 1.5мм. в основном многоэтажные пресса имеют производительность от 50 тыс до 300 тыс кубов. На бес поддонном оборудовании как правило для укрепления ковра при транспортировки стоит подпрессовщик, за счет этого производительность больше. Очень часто китайцы изготавливают именно бес поддонные линии для дсп.
4) Каландровый пресс обладает одним недостатком, плита получаемая с пресса имеет незначительную покоробленность, возникающую из — за особенностей прессования. Прессованная плита в каландровом прессе, как видно на картинке, изгибается на барабан.

Схема прессования каландровым прессом.
5) Сейчас очень много осуществляется монтажей новых мини заводов ДСП. В основном это многоэтажные линии китайского производства. Их производительность небольшая до 50 тыс... Про качество их ничего написать не могу, я на них не работал.
Очень много монтируется и работает в России старых линий, линии примерно 80-х годов. Стоимость старых линий конечно меньше, но вот работать на них конечно труднее, придется поменять все редуктора, все подшипники, валы на шлифмашине, клапана на гидравлике, в общем все маленькие детали. На это все нужно время.
Если вы определились что будете брать линию дсп. На что необходимо смотреть? Я опишу на мой взгляд маленькие но важные истины с технологической точки зрения:
- Чем больше бункера стружки, тем лучше для производства. Связано это с тем что если вы хотите чтобы линия работала на 100% мощности то каждый участок у вас должен работать на 130% мощности. Если происходит небольшая поломка допустим на сушильном отделении, то чтобы пресс не останавливался ему необходим запас сухой стружки. И если запаса хватает на 1-1.5 часа работы то это даже очень неплохо.
- Как я уже писал ранее, после пресса просто очень желательно чтобы была возможность хранения нешлифованной плиты.
- Пресса лучше одноэтажные периодического действия или непрерывные.
- Пресс для дсп выбирать лучше тот на линии у которого можно варьировать конечные размеры плиты хотя бы по длине, отсюда следует что многоэтажные пресса имеют недостаток сказывающийся на конкурентоспособности, это невозможность варьировать конечные размеры.
- Котельная лучше чтобы обогревала пресс термомаслом. Обогрев паром не есть очень хорошо.
- Котел должен нагревать масло в рабочем режиме до 250-300 градусов, при этом мощности должно хватать на то чтобы цикл прессования был 3 мин. и менее. Для этого смотрите паспорт пресса, там указывается его потребление тепла, затем делаете запас мощности 10-15% и выбираете котел.
- Горелка на сушилке лучше чтобы работала на газу и шлифовальной пыли. Мазутную горелку хлопотно зимой обслуживать. При этом конечно нужно учитывать тот факт имеются ли у вас природный газ, так как сжиженный газ это дорого. Горелку лучше брать с возможностью полной работы на пыли. Современный горелки могут разжигаться на газу а затем переходить полностью на топливо пыль. Если у вас имеется возможность работы на пыли горелки, то лучше чтобы сито имело возможность отсеивания самой мелкой стружки для горелки. Если вы сможете обеспечить пылью горелку, то экономия будет колоссальная. Но если при первоначальном расчете выйдет что вам дешевле в качестве топлива использовать газ, то с пылью вообще не стоит заморачиваться.
- Доставка смолы может осуществляться автотранспортом и ждтранспортом. Дешевле ждтранспортом. Необходим жд тупик.
- Необходимо иметь емкости под запас смолы на 10-15 дней. Если планируете варить смолу сами, то нужны еще и емкости под форконцентрат
- Лучше сразу брать линию с управлением контролером, релейные схемы давно устарели, либо можно при монтаже по максимуму все посадить на управление контролером и должна быть визуализация всех процессов, см. статью о автоматизации.
- При выборе линии обратите внимание на количество транспортеров и редукторов на переходе с одного участка на другой, если с одного участка на другой участок стружка подается через пять транспортеров, то это не есть хорошо, так как вам прийдется обслуживать не один транспортер, а пять. Это и энергозатраты, это и запасные части, это и увеличение вероятности выхода транспортера в пять раз. Здесь лучше такой принцип, чем проще тем лучше.
- Лучше линии где меньше вентиляторов и больше транспортеров, это будет способствовать экономии электроэнергии.
- Имеются линии с подпрессовщиком (нагревает ковер и без нагрева) и без подпрессовщика. Преимущество линии с подпрессовщиком это то что пресс поднимается на меньшую высоту, и вследствии этого сокращается цикл прессования. Если имеется необходимость разгона линии то установка подпрессовщика это как один из вариантов.
- Отделение клеесмешения лучше проходного типа чем периодического. Периодическое приготовление связующего это когда связующее (смола и отвердитель) готовится в емкости и затем подается в смесители, при такой подаче большое количество дорогостоящей смолы при остановках приходится выкидывать, так как смола с отвердителем быстро застывает. При проходном типе оборудования смешение смолы с отвердителем происходит в смесителе и выбрасывать связующее при остановках не нужно.
- Очень много, практически все, зависит от квалификации кадров, поэтому для отладки производства нужны очень грамотные специалисты
Удачи и до новых встреч!
andreynoak.ru
Технология по изготовлению плит дсп. Технология изготовления дсп
Для многих успешных бизнесменов не секрет, что производство ДСП в современное время - дело весьма прибыльное. Исходным материалом для изготовления ДСП являются отходы деревообрабатывающей промышленности - опилки, щепки и другие мелкоизмельченные древесные остатки. Применение такого материала во многих отраслях строительства и мебельного производства позволяет сохранять леса от дополнительной вырубки. Таким образом, сберегается зеленая зона на больших территориях, а это чистый кислород для всего человечества.
К сожалению, человек еще не придумал полноценного заменителя древесины для различных производств, вот и рубят лес, и щепки летят. В плане доступного исходного материала бизнес на производстве ДСП, безусловно, выгоден - дешевые отходы деревообрабатывающей промышленности, лесопильных цехов и большая сфера применения произведенной продукции. Процесс сбыта изготовленной продукции будет обеспечен спросом на 100 %.
При производстве ДСП можно организовать бизнес с различными направлениями: есть возможность сформировать широкомасштабный процесс производства, или же разбить его на составляющие по отдельным видам:
- Вначале, можно предложить подготовительный процесс автоматизировать.
- Отходы древесно-стружечного производства должны быть доставлены в цех подготовки. В этом цеху находится отлаженная непрерывная линия из рубильных машин и стружечных станков.
- В конце такой линии выходит технологическая щепа.
- Цикл подготовки производства закончен, и щепа может направляться в цех по производству ДСП.
Сам цех подготовки является экологически чистым, и может быть выделен отдельной структурой бизнеса.
Оборудование для производства ДСП
Следующим этапом пути отходов будет завод по производству дсп.
- Технология изготовления плиты заключается в смешивании технологической щепы и термореактивной смолы - загустителя.
- Далее смесь поступает в специальные формы различных видов и под воздействием температуры и высокого давления происходит прессование плиты, где она склеивается в единый и прочный пакет.
- После охлаждения изделия, его достают из формы и обрезают края.
- Плита готова к употреблению.
- Ее шлифуют, сортируют и, при необходимости, ламинируют.
На всех этапах необходимо технологическое оборудование для производства дсп, которое применяется в цехе подготовки производства, в основном цехе и цехе шлифования.
- В цехе подготовки производства устанавливается дробительная установка и стружечный станок.
- В основном цехе - термические пресса, веерные охладители и станки автоматической обрезки краев листа по ширине и длине.
- Для выполнения шлифовальных операций устанавливаются шлифовальные станки.
Расчет мощности и ширины обработки рассчитывают для каждой партии отдельно или вводится стандарт по данным показателям, от которого зависит сортность выпускаемого листа - это оборудование относится к основному.
К дополнительному оборудованию относят вибросита и транспортеры - ленточные, роликовые, спиральные и цепные. Применяются подъемные столы для укладки листов в пачки. Во всех цехах устанавливается вентиляционная система для сбора и удаления технологической пыли. Производство ламинированного дсп является, можно сказать, завершающим этапом. Из первого сорта шлифованной плиты изготавливают ламинированный лист или покрывают шпонкой. Ламинированный лист по цене на порядок выше шлифованного. Поэтому для производства экономически выгодно изготовление ламинированного листа. Его широко применяют отделочники для монтажа различных настилов.
Мебельная промышленность является основным потребителем ламината для изготовления дверей, фасадов, в вагоностроении он применяется как отделочный материал для перегородок, готовят из него заготовки для модульной мебели.
Ламинированный ДСП изготавливается на основе исходного материала, который значительно дешевле других материалов, технологически выгоден, а кроме того, требует меньше труда и затрат. Подготовленную и осмоленную щепу закладывают в формы, додают затвердители и необходимые в технологическом процессе добавки, после чего подают в станок для производства дсп - термические пресса. Под высоким давлением и высокой температурой происходит прессование и склеивание смеси в однородную плиту. При закладке материалов в смесители строго регламентируются весовые доли смолы и щепы. При изменении весовых долей вкладываемых материалов резко меняются физические и механические свойства полученного листа. Это приводит к изменению качества и прочности плиты. Чтобы качество изготовленной плиты соответствовало стандартам, термические пресса необходимо подбирать с автоматической настройкой, те, что обеспечивают более высокие технологические характеристики произведенных листов.
Приблизительные затраты на организацию производства ДСП
Выпуском линий для производства ДСП занимаетс
jtcase.ru
- Разведения кроликов
- Производство пластиковых ведер
- Производство ведер пластиковых
- Технология приготовления творога в домашних условиях
- Линия по производству топливных брикетов
- Гофрокартон производство
- Сколько стоит открыть бургерную
- Изготовление цемента
- Как раскрутить услуги сервиса компьютерной техники
- Производство колбасы в домашних условиях
- Как открыть гостиницу
© 2005-2018, Национальный Экспертный Совет по Качеству.