Производство пеноблоков технология и оборудование. Технология производства пеноблоков
Технология производства и изготовления пеноблоков
Производство пенобетонных блоков состоит из нескольких основных стадий, таких как: затворение пенобетонной смеси, формовка, сушка, распалубка, распиловка, термообработка, упаковка, складирование и так далее. В зависимости от выбора технологии изготовления пеноблоков и имеющегося оборудования, производители используют различные комбинации и варианты перечисленных стадий. Начнем по порядку.
Производство пенобетонной смеси
Современное производство пенобетонной смеси можно поделить на два основных вида: баротехнология и получение пенобетона с помощью пеногенератора. Каждая из технологий имеет свои плюсы и минусы. Первая более проста и экономична. Вторая более затратна, но позволяет получать пенобетон более высокого качества. Более подробно об плюсах и минусах этих двух технологий Вы можете прочитать в разделе производство пенобетона.
Формовка пеноблоков
На сегодняшний момент существует две основных технологии получения готовых пенобетонных блоков: литьевая и резательная.
Литьевая технология Литьевой способ производства пеноблоков очень похож на классическое изготовление изделий из железобетона, при котором готовая бетонная смесь отливается в металлическую форм-оснастку, сушится до набора необходимой прочности и затем вынимается из форм уже в виде готового изделия.
При производстве пеноблоков по литьевой технологии используются кассетные формы, представляющие из себя металлический поддон со съемными бортами и переборками, делящими форму на несколько отдельных секций. Похожая кассетная форма для приготовления льда лежит у Вас в холодильнике. Почти такая же применяется и на производстве пенобетонных блоков, только из металла, разборная и размером побольше. Чаще всего используются кассетные формы высотой 600 мм.
Главными минусами литьевой технологии являются:
- Неудовлетворительная геометрия готовых пеноблоков. То есть, габариты пенобетонных блоков по высоте, длине и ширине "пляшут". Происходит это из-за смещения металлических переборок при заливке пенобетонной смеси в кассету. Как правило, переборки сделаны из тонкого металла и при неравномерной заливке они могут смещаться, деформироваться и т.д.
- Наличие так называемой "горбушки". Горбушка образовывается в верхнем слое залитой кассеты. Для примера вспомните кубики льда из холодильника, верхняя часть которых имеет неровную поверхность. Аналогично образуется неровность и на поверхности застывшего пенобетона. Многие наверное помнят верхнюю часть плит перекрытий и тому подобных железобетонных изделий, у которых все стороны ровные кроме одной - верхней, которая не "обжимается" опалубкой. Горбушку на пеноблоках, изготовленных по литьевой технологии, почти всегда можно обнаружить на одном из торцов.
- Необходимость использования специализированных переборок для кассет, заточенных под конкретный размер пеноблоков. Для того, чтобы выпускать три-четыре размера пенобетонных блоков, производители должны иметь несколько видов переборок с разными размерами ячеек.
- При распалубке кассет происходит частичное повреждение углов и поверхностей готовых блоков. Происходит это из-за прилипания пенобетона к стенкам кассеты, так как к моменту распалубки пенобетон не успевает набрать достаточной прочности. Время-деньги. Нужно побыстрее вынуть едва вставшие блоки, чтобы залить очередную партию.
Отчасти повреждение готовых блоков при распалубке происходит из-за некачественной смазки блок-формы перед заливкой. По технологии полагается применять специальные смазки, которые стоят определенных денег. В условиях тотальной экономии на всем, для смазывания форм-оснастки производители зачастую используют отработку и прочую масляную дрянь, которую можно смело назвать ложкой дегтя в нашей бочке пенобетонного меда, потому как даже тяжелые бетоны имеют низкую стойкость к разрущающему действию машинных масел.
Из плюсов литьевой технологии производства пенобетонных блоков можно выделить лишь экономическую выгоду для производителя: отсутствие необходимости приобретения дорогостоящего резального оборудования и простота процесса. Впрочем, для конечного потребителя это преимущество не имеет никакого значения.
Резательная технология Подобный способ производства пеноблоков состоит из двух ступеней: отливка массива пенобетона в большую форму и его распалубка с дальнейшей резкой на блоки заданного размера. Происходит это на специальных резательных установках. В различных типах резательных установок используются разные виды режущих элементов. Это могут быть специальные струны, ленточные и цепные пилы.
Эта технология производства пенобетонных блоков обладает целым рядом преимуществ. Вот основные из них:
- Великолепная геометрия поверхностей получаемых пеноблоков, соответствующая требованиям ГОСТ 21520-89. Благодаря этому, блоки можно монтировать на клей с минимальной толщиной шва.
- На гранях и углах пеноблоков отсутствуют сколы и неровности. Этот нюанс особенно важен для сокращения расходов и трудозатрат при дальнейшей отделке стен.
- За счет отсутствия на поверхностях блоков остатков смазки (а тем более масляной обработки) которой смазываются формы-кассеты, готовые стеновые блоки обладают хорошей адгезией и привлекательным внешним видом. И если внешние данные не столь важны, то хорошая адгезия пеноблока - один из важнейших критериев успешного оштукатуривания или шпатлевания стены при проведении внешней и внутренней отделки дома.
- Возможность изготовления пеноблоков произвольных размеров. Перенастройка шага пильных струн позволяет нарезать готовые блоки по размерам заказчика.
- Благодаря обрезке массива пенобетона со всех сторон, решается и проблема с пресловутой "горбушкой" на торце блока. Она просто срезается.
Впрочем, есть у резательной технологии и свои неприятные моменты. При использовании разных видов режущих элементов должны быть четко соблюдены определенные требования к своевременности проведения резки. При резке струнами важно поймать момент, когда пенобетон уже встал, но ещё не набрал "лишней" прочности. Если этот момент прозевать, при проведении разрезки массива, струна может смещаться, уходить, что отрицательно скажется на окончательной ровности блока.
При разрезке пенобетона ленточными пилами массив наоборот должен иметь более высокую прочность, так как при резке он кантуется (переворачивается на резальном столе). И если прочность будет недостаточной, он просто будет ломаться при кантовании.
Перечисленные проблемы скорее досаждают производителям пенобетонных блоков, нежели их конечным потребителям. В любом случае, Ваша главная задача - сделать правильный выбор.
Сушка пеноблоков и набор прочности
При производстве блоков из пенобетона литьевым способом возможны две технологии первоначальной сушки изделий. Первый вариант - естественная сушка, подразумевающая 10 часовой набор прочности пенобетона в форме и его дальнейшая распалубка. Второй вариант - термическая обработка пенобетонных блоков в пропарочной камере. В отличие от естественной сушки, пропарка в камере позволяет пенобетону за несколько часов набрать 65-75% расчетной прочности.
Стоит заметить, что по подобной технологии производятся почти все железобетонные изделия. Группа BESTO поставляет пеноблоки, произведенные с применением термо-влажностной обработки в пропарочных камерах. Производство пеноблоков расположено на территории завода ЖБИ-16 в Москве.
Резательная технология производства пенобетонных блоков подразумевает естественную сушку массива в течение 4-14 часов с дальнейшей его разрезкой. Время сушки перед разрезкой зависит от использования того или иного вида режущих элементов (струны, ленточные пилы, цепи), а так же ускорителей твердения, добавляемых в пенобетонную смесь при затворении.
www.avtobeton.ru
пенобетонная смесь, формовка, сушка (Видео)
Технология производства блоков из пенобетонной смеси включает в себя несколько основных стадий:
- приготовление пенобетонной смеси;
- формовка;
- сушка;
- распалубка, нарезка, термообработка.
Каждая из этих стадий может иметь свои особенности в зависимости от выбранной технологии и оборудования на конкретном предприятии. Рассмотрим по порядку все нюансы на каждом этапе производства и их влияние на качество конечного продукта.
Производство пенобетонной смеси
В современном производстве существует два основных способа приготовления пенобетонной смеси, отличающиеся очередностью ввода основных компонентов и способом затворения пенобетонной массы.
- Классический способ с применением пеногенератора по своей основной сути можно описать так: пенная смесь готовится отдельно в пеногенераторе и затем вводится в готовую бетонную смесь, перемешивается и по трубопроводам с помощью насосов отправляется в формы.
- Баротехнология — при этом способе все компоненты пенобетонной смести (цемент, песок, концентрат пенообразующей смеси, вода) подаются в герметичный смеситель. Компрессором нагнетается воздух, создавая давление внутри смесителя, и начинается процесс перемешивания, при котором раствор насыщается воздухом. Далее, готовая смесь под давлением подается в литьевые формы, где происходит ее вспучивание в результате перепада давления.
И тот, и другой способ предполагает возможность использования различных добавок и пластификаторов. Первый способ требует более дорого технологического оборудования, а второй считается более перспективным, поскольку имеет возможность использовать искусственные добавки для вспенивания, а сам процесс выполняется быстрее. Однако, качество пенобетона, приготовленного по первому способу, пока еще остается выше и это отражается на цене.
Формовка пеноблоков
Для получения пеноблоков нужной формы и размеров используется две основных технологии: заливка в формы необходимого размера или нарезка из цельного монолита.
Литьевая технология формовки пеноблока
Литьевая технология близка к классическому способу производства подобных строительных материалов, когда готовая смесь заливается в подходящую форму, подсушивается, затем вынимается и доводится до готовности (сушка, обжиг, шлифовка).
В производстве пеноблоков используются металлические кассетные формы, со съемными бортами и переборками между секциями. При изготовлении кассет для литья пеноблоков выдерживается основной размерный параметр — высота формы 600 мм.
К несомненным достоинствам этого способа можно отнести то, что после распалубки на выходе имеется уже готовый продукт, требующий только досушки и упаковки. На практике же можно столкнуться с немалыми трудностями. Прежде всего, форма должна быть изготовлена из качественного материала, включая переборки. Качественные формы могут быть изготовлены из дорогой толстой листовой стали. Использование формы с тонкими переборками может привести к нарушению геометрии, когда при заливке пенобетонной смеси под давлением может произойти смещение или деформация переборки.
Для того, чтобы распалубка происходила безболезненно, форма требует смазки. Технология предполагает использование специальной смазки, довольно дорогой, потому производители иногда используют масляную отработку. Получатель такой продукции рискует получить остатки смазки на пеноблоке, что в дальнейшем повлияет на качество схватывания материала при кладке и отделке. Следует заметить, что низкокачественное машинное масло может оказывать пагубное действие даже на высокомарочные бетоны.
Кроме того, технология требует определенного времени выдержки, созревания пенобетонной смеси, после которой ее можно вынимать из формы без риска повредить. При ограниченном количестве кассет на предприятии есть соблазн этот процесс ускорить, что может повлиять на качество продукта, его крепость; есть риск получить блоки с поврежденными углами и поверхностями.
Еще один недостаток с точки зрения потребителя, это образование так называемой «горбушки» на верхнем слое залитой кассеты. Собственно, избежать «горбушки» не удается при любом способе литья и застывание при открытом верхнем уровне. Достаточно вспомнить обычную кассету для застывания льда в домашнем морозильнике. Тоже самое происходит и, например, с железобетонными плитами перекрытия, где гладкие и ровные стороны все, кроме одной верхней.
С точки зрения производителя недостатком литьевого способа можно считать ограниченность производства по размерам пеноблоков. Число вариантов зависит от имеющегося набора кассет. Рассчитать потребность форм того или иного размера, можно изучив рынок потребления, но и держать дорогие формы для выпуска небольших партий может оказаться невыгодным.
2. Нарезка блоков. Этот способ выполняется в два этапа:
- заливка пенобетонной массы в большую форму, просушка и распалубка;
- разрезание монолитной бетонной плиты на блоки нужного размера.
Для разрезания требуется специальная установка, в качестве ржущих элементов могут использоваться специальные струны или ленточные и цепные пилы. Этот способ обладает целым рядом достоинств, как для производителя, так и для потребителя. Вот основные из них:
- Возможность перенастройки установки для разрезания дает возможность выпускать блоки произвольных размеров по требованию заказчика.
- Высокая геометрическая точность, включая форму и размеры блоков. Это дает возможность потребителю ускорить процесс кладки и последующей отделки. Кроме того, геометрически правильные блоки можно укладывать, скрепляя специальным клеем. При этом не требуется толстого слоя, необходимого для выравнивания шероховатостей, шов получается тонким и не требует дальнейшей расшивки.
- Отсутствие смазки на поверхностях блоков обеспечивает нормальную адгезию, сцепление поверхности блока с материалом, используемым для отделки (шпатлевка, штукатурка и прочее)
- Распилка гарантирует ровные боковые грани и отсутствие сколов, образованных при вынимании блока из формы. Также в процессе распилки монолита срезается «горбушка».
К недостаткам этой технологии следует отнести необходимость точной выдержки процесса созревания пенобетонной массы в форме. При использовании струнного устройства для распиливания необходимо следить, чтобы масса не пересохла, уже хорошо держит форму, но еще не набрала заданной прочности.
При распиливании ленточными плитами требуется наоборот, чтобы масса набрала достаточной прочности, поскольку при этом способе происходит кантование блоков на резательном столе, и в противном случае возможны сколы граней или деформация.
Сушка пеноблоков и набор прочности
Для литьевого способа формования пеноблоков возможны два варианта сушки:
- естественная сушка, при которой пенобетонная масса выстаивается в формах в течение 10-ти часов для набора прочности, далее следует распалубка;
- термическая обработка в пропарочной камере: в этом случае всего за несколько часов пенобетонная масса может набрать до 75% расчетной прочности.
Этот последний способ наиболее широко используется не только в производстве пеноблоков, но и для формования железобетонных изделий.
Для технологии, использующей нарезку монолитных плит, используется только естественный способ сушки. Время процесса просушки составляет от 4 до 14 часов и зависит от технологии нарезки, использования режущих элементов, а также от используемых добавок, влияющих на процесс затвердения.
Заключение
В заключение скажем, что хотя область применения пеноблоков в строительстве имеет некоторые ограничения, например, в многоэтажном строительстве, но тенденция использования их в маломассивном и индивидуальном строительстве способствует расширению производства и улучшению качества этого строительного материала. Однако, как можно видеть, использование разных технологий, дает на выходе разный продукт. Обращаясь в компанию по производству и реализации пеноблоков, следует познакомиться с применяемой технологией. Так, при классическом способе производства с помощью пеногенератора, используются только биологические добавки для производства пенной массы, а конечный продукт — действительно экологически чистый строительный материал. Зная способ формования блоков, можно оценить насколько трудоемкой окажется кладка и последующая отделка.
Материалы по теме:
moscowsad.ru
Оборудование + Технология как делают 2018

Впервые пенобетон появился в тридцатых годах прошлого века. В то время советский ученый, строитель-экспериментатор Брюшков, добавил к цементному раствору мыльный корень. Таким образом, был получен новый строительный материал. Спустя годы специалисты стали пробовать смешивать цемент с различными химическими добавками – пенно и газообразующими веществами, а именно: с алюминиевой пудрой, с клееканифольным раствором.
Ниже представлена информация про производство пенобетона, оборудование и технологию изготовления с видео как делают. Коротко и подробно о самом главном в этом бизнесе.
Технология производства пенобетона
Общая информация
Технология его изготовления основывается на смешении предварительно подготовленной пены с растворной смесью. Что касается концентрата пенообразователя и воды, то при получении пены они дозируются по объему. После этого готовый раствор смешивается и, таким образом получается пенообразователь для пенобетона. Далее производство пенобетона происходит следующим образом: пенообразователь подается в пеногенератор, в котором осуществляется образование пены. После этого в бетоносмеситель передается пена из пеногенератора и данная смесь перемешивается примерно от трех до пяти минут. Затем, уже готовый пенобетон транспортируется через гибкий рукав к месту, в котором производится укладка его в форму или опалубку.
Расход компонентов при производстве
На приготовление 1 кубического метра пенобетона требуется 500 килограмм цемента. Для приготовления пенобетона с плотностью 300 килограмм на кубический метр необходимо 270 килограмм цемента. Давайте рассмотрим, какие необходимо материалы для приготовления пенобетонной смеси. Во-первых, цемент. Во-вторых, заполнители. Крупными заполнителями являются: щебень, а вот гравий не нужен. Иногда возможно добавление легкого заполнителя, такого, как керамзит. В этом случае прочность пористого бетона возрастает примерно на 100 – 200 процентов. Мелкими заполнителями являются: природные или дробленые пески. А наиболее предпочтительным считается речной песок. Данный наполнитель должен быть обязательно чистым, не содержащим различных включений.
Для выполнения укладки используются пески мелкой фракции примерно 0,2 миллиметра. Что касается глинистых включений, то они не должны превышать более 3 процентов. В-третьих, вода. Производство пенобетона требует использовать воду без всякой проверки. Содержание воды в пористом бетоне состоит из расчетного количества. Так, перед тем как добавлять пену, водоцементное отношение раствора должно равняться минимум 0,38. При слишком низком значении водоцементного отношения, пенобен получиться с более высокой объемной плотностью. Это может произойти в результате того что бетон станет забирать из пены требуемую для химических и физических взаимодействий воду, при этом частично станет разрушаться пена, а это приведет к снижению ее объема в пенобетонной смеси. Наиболее оптимальным является соотношение, находящееся в интервале от 0,4 до 0,45. При этом температура воды не должна превышать 25 градусов.
Специалисты советуют в качестве пенообразователя использовать для производства протеиновый пеноконцентрат. Данное вещество необходимо сберегать в герметично закрытых деревянных или пластмассовых бочках. Такие бочки должны быть скрыты от попадания на них прямых солнечных лучей. А также они должны храниться при температуре не выше +30 градусов. Пеноконцентрат с момента приготовления может сберегаться от 15 до 30 суток.
Получение пенобетонной смеси + видео как делают
При приготовлении смеси, прежде всего, засыпается песок, который должен связать воду, после этого добавляется цемент и все тщательно перемешивается до образования однородного цвета смеси. Достаточно важным является хорошо распределить цемент в песке. Затем в смесь доливается вода, в том количестве, которое указано в выбранной рецептуре. Смесь перемешивается до тех пор, пока не будет получена однородная пластичная масса.
Особое внимание следует обращать на качество перемешивания компонентов. Только равномерное распределение цемента в песке позволит получить оптимальное качество пенобетона. После всего ранее перечисленного, при помощи пеногенератора определенная порция пены подается по шлангу в смеситель, где на протяжении 120 — 180 секунд она перемешивается с предварительно подготовленной цементно-песчаной смесью. Если контролировать задаваемую плотность, то можно достаточно легко получить требуемую прочность пенобетона на сжатие. Литому пенобетону, как и любому иному, который связан цементом, необходимо создать температурно-влажностный режим. Это выполняется, с одной стороны, для поддержания процесса гидратации цемента, набора прочности, с другой стороны, снижает температуру экзотермии и не дает образоваться трещинам в бетоне. Из-за этого, рекомендуется сразу же после укладки смеси накрывать бетонную поверхность полиэтиленовой пленкой.
Видео как делают:
Области, в которых используется пенобетон
Данный материал применяется на крышах и полах как тепло- и звукоизоляция. Сам по себе пенобетон не является конструкционным материалом. Кроме этого он используется для теннисных кортов и заполнения пустот в кирпичной кладке подземных стен, изоляции в пустых пустотелых блоках и любом другом заполнении, где требуются высокие изоляционные свойства. Областью использования пенобетона является: производство строительных блоков, для классического строительства домов и перегородок, монолитное домостроение тепло- и звукоизоляция стен, полов, плит, перекрытий, заполнение пустотных пространств.
Читайте также
moybiznes.org
Производство пеноблоков технология и оборудование
Бизнес производство пенобетонных блоков. Пеноблоки: технология производства, оборудование.
Пеноблок (пенобетонный блок) – строительный материал с пористой структурой на основе вспененного бетона, изготовляется по классической или баротехнологии из смеси на основе пены и бетона.
Наиболее распространённые типоразмеры пеноблоков:
- 600×300х200.
- 600×300х150.
- 600×300х100.
- 500×300х200.
- 500×300х150.
- 500×300х100.
Пенобетон подразделяется по основным свойствам и характеристикам на несколько видов:
- Теплоизоляционный.
- Конструкционно-теплоизоляционный.
- Конструкционный.
Теплопроводность пенобетона таблица.
Морозостойкость, класс по прочности на сжатие.
Оборудование для производства пеноблоков.
Комплект оборудования зависит от технологии производства, если используется классическая технология, то установка для производства пеноблоков будет состоять из оборудования:
- Смесителя.
- Пеногенератора.
- Форм для отливки.
Для производства пенобетонных блоков по баротехнологии понадобится следующие оборудование:
- Бароустановка.
- Формы для отливки блоков.
Производственная линия.
Сырье для производства пенобетонных блоков.
- Портландцемент М500Д20, М400Д0, М400Д20, если используется баротехнология то понадобится цемент марки М500Д0.
- Песок ГОСТ 8736-93. (вместо песка можно использовать известняковую или доломитовую муку, отсев).
- Фиброволокно (армирующий элемент).
- Вода ГОСТ 23732-79.
- Пенообразователь (синтетический для бароустановки или белковый для классической).
Технология производства пеноблоков.
Для производства пеноблоков применяется два варианта технологий:
Классическая.
Классическая технология основана на использовании пеногенератора. В пеногенераторе приготавливается пена, а в смесителе подготавливается бетонная смесь. Затем пена добавляется в бетонную смесь, полученный состав заливается в формы где и застывает.
Баротехнология.
В баротехнологии для приготовления пенобетона применяется бароустановка (герметичный высокооборотистый миксер). При замешивании смеси в бароустановку подаётся под давлением сжатый воздух и компоненты для раствора, таким образом в бароустановке производится пенобетонный раствор который и разливается шлангом в формы для отливки.
Плюсы такой технологии в дешевизне и в простоте производства, минусы в повышенном расходе пенообразователя и меньшая прочность получаемого пенобетона по сравнению с классической технологией.
Независимо от технологии производства, чтобы получить блоки из пенобетона применяется один из двух вариантов.
Заливка пенобетона в формы с перегородками.
Получение блоков методом заливки пенобетона в кассетные формы, пенобетон застывает 2 — 3 суток, после чего форма разбирается и извлекаются готовые пеноблоки.
Второй метод резка пенобетона.
Пенобетон отливается в форме в один массив объёмом около 2 куб. м затем на резательной установке его распиливают пилами на блоки.
Производство пеноблоков.
Рассмотрим процесс изготовления пенобетонных блоков по классической технологии.
Подготовка форм для отливки.
Разборные металлические формы для отливки собирают и покрывают смазкой, в качестве смазки используется эмульсионный разделительный состав.
Приготовление бетонной смеси.
Сначала в смеситель заливается вода и добавляется фиброволокно, затем добавляется цемент и наполнитель (песок).
В это время отдельно готовится концентрат, в пенообразователь добавляется вода, смесь перемешивается и заливается в пеногенератор.
В бетонный раствор добавляется приготовленная пена, смесь перемешивается до однородной консистенции.
Заливка форм.
В подготовленные и смазанные формы заливается пенобетонная смесь.
Выдерживание.
Чтобы пенобетон набрал необходимую первоначальную прочность ему нужно выстояться в формах не менее 3 суток, после чего его можно будет укладывать на поддоны.
Распалубка или резка.
На данном этапе пенобетон набирает достаточную прочность, чтобы его можно было извлекать из форм или распиливать массив на блоки.
Производится распалубка форм, блоки извлекаются, укладываются на деревянные поддоны, после чего блоки нужно обмотать стрейч плёнкой чтобы бетон быстро не терял влагу.
Для окончательного набора прочности блоки нужно ещё оставить на 28 дней на складе, после чего их можно отправлять на продажу и использовать для строительства.
Производство пеноблоков видео.
На видео показан процесс производства пенобетонных блоков.
Преимущества применения пеноблоков в строительстве.
Пенобетонный блок обладает высокой прочностью.
Экологичность. Пеноблоки не выделяют вредные вещества, коэффициент пенобетона по экологичности – 2, дерева – 1, кирпича – 10.
Обладает высоким термическим сопротивлением, помещение из пеноблоков способно аккумулировать тепло в холодный период и удерживать прохладу в летний зной.
Пенобетон способен регулировать влажность воздуха в помещении, путём впитывания и отдачи влаги по аналогии помещений из древесины.
Скорость монтажа. Благодаря большим размерам и сравнительно лёгкому весу блоков скорость кладки возрастает в несколько раз по сравнению с кирпичной кладкой.
Лёгкость в обработке. Пенобетон достаточно легко поддаётся обработке, его можно распиливать на нужные куски, делать каналы под электропроводку, трубы.
Звукоизоляция. Пеноблоки обладают достаточно хорошим поглощением звука, помещение из пенобетона полностью соответствует требованиям звукоизоляции.
Популярные бизнес идеи
Переработка шин в крошку: техн...
Бизнес прачечная самообслужива...
Производство резиновой плитки ...
Производство искусственного ка...
Производство бетонных заборов...
Как открыть блинную: документа...
Бизнес на малине: выращивание ...
Корн дог бизнес
Разведение карпов бизнес...
Разведение осетра...
Резьба по дереву бизнес...
Кондитерский бизнес...
biznes-proizvodstvo.ru
Технология производства пенобетона
Пенобетон – это разновидность бетона, имеющая ячеистую структуру. Благодаря тому что в ячейках находится воздух, основным качеством является отличная теплоизоляция. Этот материал имеет такую высокую текучесть, что его легко заливать в формы, получая заготовки различного вида.
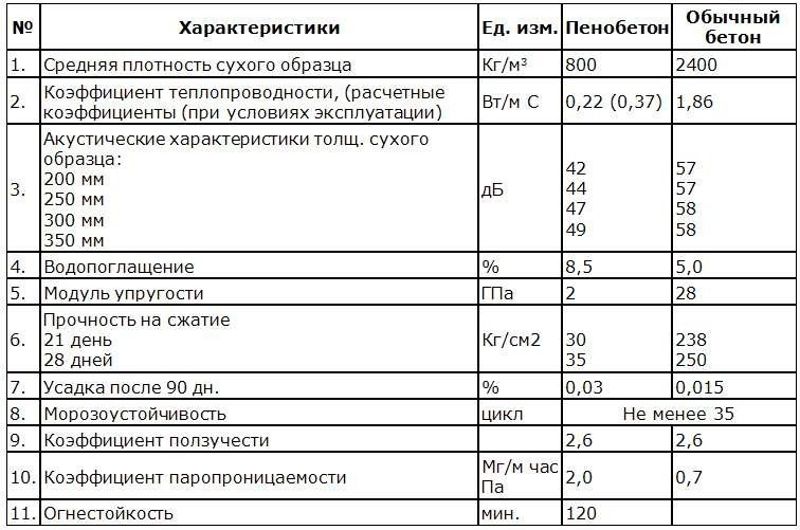
Сравнительная таблица характеристик
Две эти характеристики обусловили широкое применение пенобетона в строительстве. Из него выполняют различные строительные изделия – перегородки, стеновые блоки, плиты перекрытия и многое другое. Востребован данный материал и для изготовления пола и кровли. Особенно широкое применение нашел он в малоэтажном строительстве.
Пенобетон, технология его изготовления настолько проста, что при желании ее легко воспроизвести даже в домашних условиях.
Вся схема производства разделена на 3 этапа: изготовление цементно-песчаной смеси; приготовление раствора пенообразователя и получение смеси.
В зависимости от того, какой плотности материал необходимо получить, выбираются пропорции составляющих компонентов. Технология приготовления, в зависимости от соотношений песка, цемента, воды, а также концентрата пенообразователя или пены, позволяет получать плотность пенобетона от 200 до 1500 кг на 1 м3. При приготовлении средней плотности предусмотрено соотношение песка и цемента 1:1. Причем на каждый кг цемента берется 3-4 г концентрата пенообразователя.
Цементно-песчаная смесь
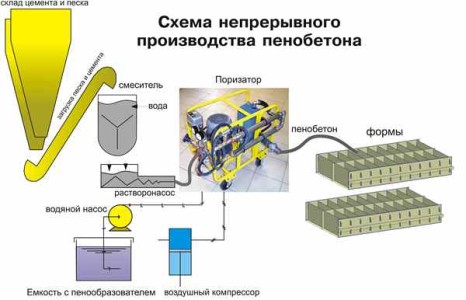
Схема непрерывного производства пенобетона.
Цементно-песчаную смесь для приготовления пенобетона готовят аналогично той, которая используется при производстве обычного бетона. Для нее выбирается портландцемент марок М400 или М500. Используемый песок, имеющий модуль крупности не более двух единиц, должен быть без глиняных примесей, так как они будут препятствовать сцеплению цемента и песка. Для приготовления цементно-песчаной смеси применяется обычная водопроводная вода, не содержащая в своем составе кислот и солей.
Виды и целесообразность применения
К пенообразователям, применяемым при приготовлении, предъявляются определенные требования, основное из которых – технико-экономический показатель. В денежном выражении, независимо от изготавливаемого пенобетона, его стоимость не должна превышать 2$ на 1 м3 готовой продукции. Более дорогой пенообразователь приводит к удорожанию себестоимости пенобетона. Причем он не способен увеличить качество продукции пропорционально увеличенной стоимости.
Вне зависимости от партии и срока выпуска, пенообразователь должен иметь одинаковые свойства, чтобы не приходилось постоянно перенастраивать оборудование в технологической линии, что, в свою очередь, может привести к снижению качества готовой продукции.
Данный компонент должен иметь достаточный срок годности. Если срок его хранения менее одного года, то придется в процессе производства постоянно докупать недостающее количество небольшими партиями, что экономически невыгодно. Кроме того, при завершении строительного сезона уменьшаются объемы приготовления , и пенообразователь может до следующего сезона просто испортиться.
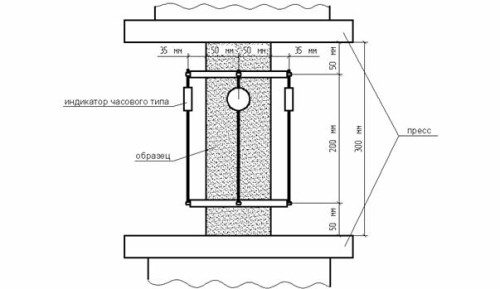
Схема испытания пенобетонных образцов.
При выборе типа пенообразователя следует обратить внимание на норму расхода. Она не должна превышать 1,5 л на 1 м3 готового раствора. Соблюдение такого условия необходимо по двум причинам. Первая – получение большего объема продукции за одну загрузку смесителя. Вторая связана с уменьшением влияния данного ингредиента на свойства продукции. Ведь при его избытке повышается время, требуемое на затвердевание пенобетона, увеличивается усадка и снижается прочность.
Еще одно требование, которое должно соблюдаться при выборе пенообразователя – простота его приготовления. Он не должен состоять из множества компонентов. Чем больше составляющих в его составе, тем более усложняется процесс его приготовления, связанный с трудностями при их дозировании. Также этот материал должен хорошо растворяться в воде.
Качество пены
От качества пенообразователя зависит стойкость пены, которая, в свою очередь, во многом определяет физико-механические свойства. Следует обратить внимание и на кратность пенообразователя, которая не должна быть менее 10.
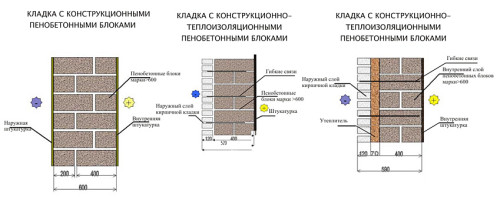
Схема кладки пенобетона в нескольких вариантах.
Пенообразователь должен обеспечивать достаточную стойкость пены при приготовлении пенобетона. Коэффициент стойкости определяется в лабораторных условиях. Чем он выше, тем меньшее количество пены требуется для изготовления продукции заданной плотности и, соответственно, меньший объем пенообразователя. Как и всякая добавка, последний в больших количествах способен не только притормозить, но и окончательно остановить процесс затвердения пенобетона. Поэтому так важно использовать пену высокой кратности.
И, наконец, последнее. Пенообразователь должен соответствовать санитарно-гигиеническим нормам – быть нетоксичным, невзрывоопасным и отвечать радиационным требованиям.
Приготовление раствора
Перемешав компоненты цементно-песчаной смеси, добавляется приготовленный раствор пенообразователя. Самыми востребованными в технологии пенобетона являются синтетические пенообразователи, которые можно приобрести на строительном рынке. Изготовленные промышленным способом, они позволяют получить более устойчивый и качественный по сравнению с другими рабочий раствор.
Но пенообразователь можно изготовить и самостоятельно. Это касается приготовления в домашних условиях. Для этого надо смешать 1 кг канифоли, 150 г едкого натра и 60 г столярного клея. Смесь из таких составляющих измельчают, нагревают и перемешивают до состояния полной однородности. Но необходимо учесть, что смесь, приготовленную по такому рецепту, можно применять, только получая пенобетон с применением парогенератора.
Итак, добавив в концентрат пенообразователя необходимое количество воды, получается готовый рабочий раствор.
Схема приготовления
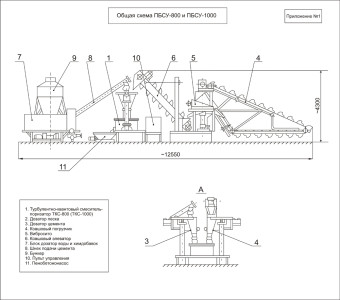
Общая схема рабочего процесса по изготовлению пенобетонной смеси.
В зависимости от вида используемого пенообразователя и принятой технологии, выбирается метод приготовления пенобетона. Но вне зависимости от способа вспенивания в основе любого технологического процесса лежит получение гетерогенной системы «газ – жидкость – твердое вещество».
При приготовлении пенобетона может использоваться два вида оборудования. В первом случае применяются пеногенераторы. Во втором – баросмесители, то есть установки кавитационного вида.
По классической схеме приготовление цементно-песчаной смеси происходит в особой емкости – смесителе принудительного типа. В этот же резервуар после приготовления смеси пеногенератором добавляется пенообразователь или пена для пенобетона. Смесь готова к заливке в формы после тщательного перемешивания.
Структура материала формируется за счет отвердевания и схватывания вяжущего компонента. Приготовленная смесь транспортируется посредством насоса в монолитную конструкцию или форму.
Изготовление в баросмесителе
При пенобетоне, технологии изготовления которого требуют кавитационной установки, все компоненты смеси закладываются в смеситель одновременно, и подача пенобетона из нее в формы или монолитную конструкцию осуществляется за счет наличия в смесителе избыточного давления. При таком способе масса в герметичном смесителе насыщается сжатым воздухом.
Технологический процесс изготовления данного материала может предусматривать какие-либо дополнительные операции, способствующие приобретению им дополнительных свойств. Это могут быть мероприятия, направленные на регулирование структуры смеси, оптимизацию ее состава, использование пластификаторов, применение наряду с пенообразователем газообразователя и подобные им.
Существуют и другие технологии приготовления, однако в настоящее время они не нашли широкого применения.
Затвердевание пенобетона
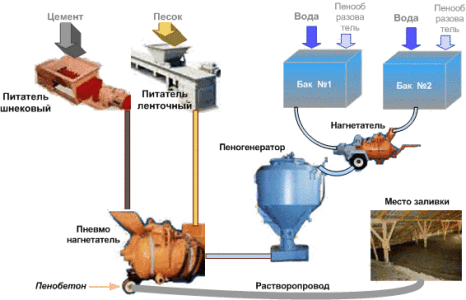
Технологическая схема производства
Для чего нужно ускорять затвердевание? Рост заданной прочности пенобетона значительно отличается от аналогичного показателя обычного бетона. Последний набирает практически стопроцентную прочность при естественном твердении. За такой же промежуток времени пенобетон способен набрать лишь половину прочности. Чтобы добрать оставшуюся часть, ему потребуется приблизительно полгода.
Если в производственном помещении температура окружающей среды менее 10 градусов, то время на затвердевание значительно увеличивается, и чтобы вынуть блок из формы, нужно ждать 2-3 дня. Для решения этой проблемы и используют ускорители затвердевания. Они могут быть различными. Но самый простой из известных ускорителей – это хлористый кальций. Он добавляется в цементно-песчаную смесь в количестве 1-2 % от объема содержащегося в ней цемента.
Существует один момент при его применении. Один из компонентов пенобетона – пенообразователь – обязан поддерживать в течение определенного времени форму пузырьков. Ускоритель в виде хлористого кальция вступает в реакцию с ним, что может привести к большой усадке пенобетона.
В настоящее время для ускорения процесса затвердевания применяются специально изготовленные препараты для пенобетона, способные ускорить процесс почти в 3 раза и выпускать данную продукцию при температуре до 5 градусов.
Выбор технологического процесса
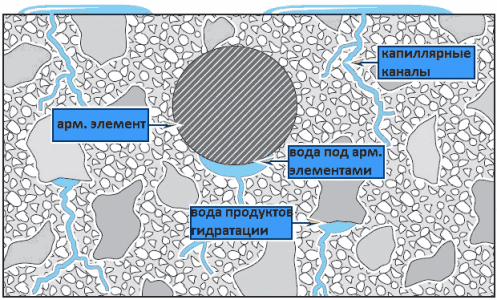
Типичная схема влажностной усадки в пенобетонах.
При выборе технологической схемы нужно руководствоваться тем, какие характеристики материала требуется получить, какие виды сырья используются и какие возможности существуют на предприятии, занимающемся приготовлением пенобетона. Любая технология должна выполняться для соблюдения основного условия – получения качественного материала с хорошо организованной пористой структурой.
В процессе изготовления пенобетона в смеси происходят такие изменения, которые способствуют приобретению его молекулярной структурой системы, состоящей из маленьких сферических ячеек размером 0,1-2 мм в диаметре. Окончательная структура пенобетона формируется при его окончательном затвердевании. В ходе технологического процесса плотность бетона легко поддается корректировке, что является незаменимым качеством при производстве материала на строительной площадке или в условиях малого предприятия.
Способы разливки
На последнем этапе пенобетон заливается в формы, опалубки или кассеты. Смазка, применяемая для форм, не должна содержать в своем составе масла, так как его наличие затруднит дальнейшее шпаклевание и оштукатуривание пенобетонных блоков. Готовые формы для получения блоков соответствующих размеров разрезают на ленточнопильном оборудовании.
На данный момент используется еще один способ получения блоков – заливка в формы. Каждый из методов имеет как свои достоинства, так и недостатки.
При кассетном методе разливки смеси технологический процесс довольно прост. При выпуске продукции до 20 м3 в день денежные вложения в оборудование будут гораздо меньше, чем при использовании других методов разливки пенобетона. Также возможно наращивание объемов производства без значительных затрат. При этом можно изготавливать уникальные модели блоков, например пазогребневые.
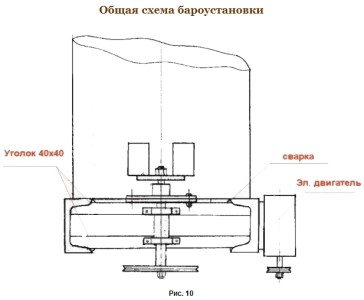
Общая схема бароустановки для производства пенобетона.
К недостаткам этого способа можно отнести невысокую производительность и применение ручного труда в больших объемах. При этом геометрические размеры готового блока получаются менее точными, а внешний вид – недостаточно привлекательным.
Другое дело – разлив смеси в массивы и последующая их резка. При такой технологии получаемые размеры готовой продукции более точные, чем при первом способе. Данный метод позволяет на предприятии выпускать большой объем продукции и легко наращивать его при минимальном вложении средств. При этом невелико использование ручного труда. К недостаткам данного способа можно отнести более высокую цену готовых пеноблоков и большое количество отходов производства.
Выбор того или иного метода зависит от требуемого количества продукции. При небольших объемах предпочтительнее использовать более простую разливку в формы, а при более значительных – резательный способ.
o-cemente.info
Технология производства пенобетона
Пенобетон – это пористый камень, который создается искусственно и имеет пористую структуру по всему объему. Размер пор достигает размера до 3 мм. Его также называют ячеистый бетон. В настоящее время в производственной промышленности пенобетона, а также изделий из него, различаются две основные технологии его получения: баротехнология и производство с использованием пеногенератора. Необходимо отметить, что в обеих методиках применяется почти одинаковое сырье, но при этом отличия состоят как в способе затворения, так и в порядке введения базовых компонентов. Благодаря этому, продукция получается разной прочности и отличается качеством.
Баротехнология
Использование метода баротехнологии в производстве данного материала отличается и преимуществами, и недостатками. Изделия, полученные методом баротехнологии, имеют низкий уровень прочности, но отличаются более простым и менее затратным процессом. Они не требует дорогостоящего оборудования и слишком больших помещений, а время получения условной единицы значительно сокращается. Данный способ получения пенобетона используется именно из этих экономических соображений. Однако, если для производителей таких стройматериалов вышеназванные качества являются плюсом, то потребитель получает низкокачественную продукцию, которая не должна использоваться в больших объемах строительства.
При применении баротехнологии, в герметичный смеситель вводят базовые компоненты камня: песок или зола-уноса, цемент, вода, ускорители твердения, пенообразователь, а иногда воздухововлекающие добавки. В технологии изготовления смесей в необязательном порядке внедряются также дополнительные операции, которые направлены на оптимизацию гранулометрического состава компонентов и регулирование пористой структуры, на применение газо- и пенообразователей, а также использование функциональных добавок, которые ускоряют структурообразование.
Затем под давлением, образующегося в смесителе, все эти компоненты тщательно размешиваются и смесь активно насыщается воздухом. Этот процесс принято называть воздухововлечением. Под давлением полученный раствор через трубопровод поступает прямо в литьевые формы. При этом останавливается процесс атмосферного давления, которое нагнеталось в смесителе с помощью компрессора, после чего пенобетонная смесь начинает увеличиваться в объеме. Визуально этот процесс напоминает всход дрожжевого теста, который отличается только скоростью «всхождения»: у этого же материала в момент формовки увеличение происходит моментально.
Достоинства и недостатки метода баротехнологии
А теперь подробнее остановимся на минусах и плюсах баротехнологии производства пенобетона. Данный метод отличается более низкой прочностью продукции, что является главным его недостатком. Конечно лучше и результативней взбивать более жидкие субстанции. Чтобы сравнить, нужно представить консистенцию взбитой 30%-ой сметаны с молоком. В состав затворения производители вынужденно вводят большее количество воды, из-за чего окончательная прочность пеноблоков значительно уменьшается. Для полноценного процесса гидратации при получение цемента большее количество воды нежелательно. Процесс гидратации — это присоединение воды, которое происходит с помощью химической реакции клинкерных составляющих цемента с водой. При взаимодействии с водой цемент твердеет и превращается в так называемый цементный камень.
При этом в пенобетоне, который изготавливается методом баротехнологии, образуются довольно крупные поры. Их можно сравнить с порами мелкой пемзы. Воздушные пустоты в его структуре редко бывают меньше 1-2 миллиметров. Естественно, такие крупные поры намного снижают прочность и несущую способность блоков в будущих конструкциях зданий.
Недостатком этого метода можно также считать применение синтетических пенообразователей, которые имеют низкую экологичность. Нужная подвижность смеси, без увеличения пропорции воды, получается добавлением пластифицирующих субстанций – суперпластификаторов. Сегодня ни одно современное предприятие цементных или бетонных смесей не обходится без специальных добавок в производстве бетона, что существенно улучшает качество смеси и регулирует процессы схватывания и твердения цемента.
Несмотря на безусловное увеличение качества и подвижности пенобетонной смеси, его применение исключает использование натуральных пенообразователей, которые используются для производства ячеистых бетонов. Известно, что они получаются в процессе превращения макромолекул натурального протеина гидролизом в водном растворе. Одним словом, если потребитель решается построить дом из экологически безопасных материалов, он изначально должен исключить использование пеноблоков, которые изготовлены методом баротехнологии.
Безусловно, существенным достоинством производства этих изделий данным методом считается более низкая себестоимость, что значительно увеличивает экономическую выгоду для производителя. Основным достоинством баротехнологии является также использование более дешевого технологического оборудования, которое не требует больших вложений и организуется в любом приспособленном для этого помещении.
Если в применении данной технологии получения бетона все плюсы достаются производителям, то описание другого метода, приведенного ниже, может стать достоинством в производстве пенобетона в угоду строителям и покупателям.
Метод пеногенерации
В первой половине 20-го века инженером Байером был изобрен новый метод производства пенобетона, который отличался от баротехнологии тем, что пена продукции подготавливалась отдельно. В его производстве методом пеногенерации различаются две стадии: приготовление пены при помощи пеногенератора и минерализация полученной пены с цементом и песком. При получении изделия с применением первого метода основные компоненты замешиваются в правильной дозировке, а процесс не придерживается принципа изменения водоцементного соотношения. Благодаря этому, изделия на выходе отличаются своей технологичностью. Главный элемент – пеногенератор, в данной технологии используется для получения мелкопористой пены из смеси воздуха, воды и пенообразователя. Последний применяется с 20-30%-ой экономией. При этом, несмотря на масштабы производства, необходима полная комплектация линии современным и качественным оборудованием, что станет гарантией высокой надежности полученной продукции, а также длительного срока службы.
Вот как происходит производство блоков методом пеногенератора. В смеситель вводятся такие точно дозированные сыпучие компоненты, как цемент и песок, иногда в качестве заполнителя можно добавлять золу-уноса. При подмене песка на последний компонент, у камня значительно уменьшается теплопроводность, что, в свою очередь, повышает теплосбережение здания. Необходимо знать, что те продавцы, для которых прибыль важнее, чем качество получаемой продукции, при их производстве используют минпорошок и золу-уноса в качестве весовой добавки. Стоимость этих компонентов намного меньше стоимости цемента.
После добавления компонентов в смеситель и их смешивание, в пеногенератор подводится сжатый воздух от компрессора. При этом персонал должен постоянно регулировать подачу рабочего пенообразователя и сжатого воздуха, от чего зависит качество пены на выходе. Этот процесс ничем не отличается от производства бетона. После приготовления техническая пена подается в специально изготовленный смеситель – пенобетоносмеситель, частота оборотов которого не более 300 об/мин. Этот этап производиться очень аккуратно, без разрушения полученной пены. Затем вводиться цемент и песок. Этот процесс называется технологией «сухой минерализации». А при «мокрой минерализации» пена подается в предварительно приготовленный раствор цемента и песка. Благодаря полному контролируемому процессу активного смешивания пены с цементно-песчаным раствором, производство пеноблоков производится на более качественном уровне.
Достоинства и недостатки метода пеногенерации
Далее приведем некоторые недостатки и достоинства в пеногенераторном процессе производства. Данный метод отличается достаточно высокой себестоимостью, когда в производстве используется дорогостоящее оборудование, и на единицу готовой продукции уходит больше времени. Параллельно этому повышается также стоимость производимых блоков. То есть более высокая цена продукции вытекает из высокой себестоимости производства.
Плюсами производства данный строительных материалов с помощью пеногенератора является более качественный массив пеноблока. Применение заранее приготовленной пены помогает производить изделие на выходе с правильной структурой, тем самым избегая появления крупных воздушных пор и стремясь к получению более высокой и равномерной прочности.
Нельзя не отметить высокую экологичность в их производстве, когда используются экологически чистые пенообразователи. Их использование в строительстве домов становиться залогом здоровья их будущих жителей.
Обобщая вышеназванные качества «пеногенераторной» технологии, можно сказать, что этот метод скорее «за» потребителя, а производители, в свою очередь, стараются его не выбирать. Баротехнология им намного выгоднее и не требует больших вложений.
Материалы по теме:
moscowsad.ru
Изготовление пенобетона: технологии, процесс, затраты
Пенобетон – материал относительно новый, но уже широко используемый в современном строительстве. Свойства пенобетона, по сути, уникальны, так как по качествам он очень схож с деревом, хотя является искусственным материалом. Стены из пенобетона «дышат», поддерживая благоприятный микроклимат в помещении, так как обладают паропроницаемостью, но, не смотря на это, водонепроницаемы, не подвержены гниению и не горючи. Пенобетон морозоустойчивый, экологичный, прочный материал, имеющий относительно небольшой вес и высокие теплоизоляционные показатели. Однако свойства пенобетона, впрочем, как и качество, напрямую зависят от технологии изготовления пенобетона.
Технология изготовления пенобетона
Выделяют два основных способа производства пенобетона. Причем, компонентный состав в обоих случаях практически не отличается, а вот сама технология изготовления пенобетона, последовательность, разнится весьма значительно — это и сказывается на качестве и эксплуатационных свойствах готовой продукции.
Баротехнология производства пенобетона
Способ производства пенобетона не требующий дорогостоящего оборудования и дополнительных временных затрат, а потому, зачастую, более популярный среди производителей. Однако качество пенобетона при данном способе производства оставляет желать лучшего. Почему?
Ответ кроется в технологии производства, а заключается она в следующем:
Все ингредиенты – цемент, песок, вода, пенообразователь, зола-уноса, добавки ускоряющие твердение, воздухововлекающие добавки — помещают в герметичный смеситель, смесь активно перемешивается и попутно в смеситель под давлением нагнетают воздух, благодаря чему раствор и насыщается воздухом. После перемешивания пенобетонная смесь попадает в литьевые формы, где и затвердевает, обретая форму.
Важно:
Основной недостаток данного способа заключается в объеме воды, добавляемом производителем для того, чтобы перемешать такую смесь, а излишки воды в дальнейшем негативно сказываются на прочности пенобетонного блока.
Конечно, некоторые производители вместо увеличения объема воды, в пенобетонную смесь добавляют пластификаторы, но применение пластификаторов ставит под сомнение экологичность конечного материала.
Таким образом, к плюсам данной технологии можно отнести лишь экономичность производства и низкую себестоимость, а к минусам:
- низкую прочность пенобетонных блоков, связанную с излишками воды во время производства и крупнопористой структурой. Как правило, воздушные пустоты в структуре пенобетона, произведенного по баротехнологии, бываю не менее 1-2мм;
- при использовании пластификаторов, производителям приходится использовать синтетические пенообразователи, что отрицательно сказывается на экологичности готовой продукции.
Производство пенобетона с использованием пеногенератора
Процесс производства пенобетона с применением пеногенератора потребует от изготовителя дополнительного оборудования и времени на производство единицы продукции, данный факт положительно сказывается на качестве пенобетона, но не экономично на стоимости и это, пожалуй, является единственным минусом.
При производстве пенобетона с использованием пеногенератора в смеситель, где предварительно замешивается песчано-цементный раствор, из пеногенератора подается уже готовая техническая пена и затем происходит перемешивание до нужной консистенции. Причем процесс полностью поддается контролю, как при замешивании песчано-цементной смеси, так и при пенообразовании в пенообразователе. В результате, качество продукции на выходе намного выше, чем при применении баротехнологии. Пенобетонные блоки получаются прочнее за счет равномерной мелкопористой структуре и экологичными за счет применения экологически чистых белковых пенообразователей.
Не смотря на то, что стоимость пенобетонных блоков произведенных по данной технологии выше, применять в строительстве именно их целесообразнее, а главное, надежнее. Ведь поговорку: «Скупой платит дважды», никто не отменял.
wallsgrow.ru
- Производители полипропиленовых мешков
- Производство рентабельное
- Производство масла
- Рентабельное производство
- Линия по производству саморезов
- Выращивание уток на мясо в домашних условиях
- Как открыть брокерскую компанию
- Аппарат для изготовления пончиков
- Открытие гостиницы
- Технология производство клееного бруса
- Технология производство клееного бруса
© 2005-2018, Национальный Экспертный Совет по Качеству.