Пенополистирол экструдированный: технология производства. Технология производства пенопласта
Технология производства пенополистирола. Сферы применения материала
[contents h3 h4]Технология производства пенополистирола.
Пенополистирол – это особый материал, изготавливаемый из полистирола и наполняемый газом. Он зачастую используется при термоизоляции, но нередко его можно встретить в составе различных конструкций. Его применяют при производстве суден, железнодорожных составов, самолетов, им упаковывают разнообразную продукцию.
Основные характеристики пенополистирола
Прежде всего, хотелось бы отметить экологичность материала. В общем, такой материал может быть экструзионным и термоударным, но вне зависимости от типа, вопрос о его экологичности спорен. Дело в том, что если использовать пенополистирол, к примеру, в конструкции стены, то для организма он будет полностью безвреден. Другое дело пожар, при котором материал будет выделять токсичные вещества. Так что при утеплении им стен дома необходимо дополнительно нанести слой штукатурки. Теперь же о других особенностях материала:
1. Долговечность – пожалуй, главная особенность. Считается, что пенополистирол способен прослужить от шестидесяти до восьмидесяти лет.

2. Также материал способен поглощать в себя воду, если непосредственно с ней контактирует.
3. Его трудно растворить в спирте, эфире и углеводах, вместе с тем он запросто растворяется, к примеру, в стироле или сероуглероде.
4. Он не пропускает пару. Абсолютно.
5. Бактерии, грибки и другие микроскопические организмы нередко основывают в пенополистироле собственные колонии. Также это могут быть насекомые, грызуны и даже птицы. Но научно доказано, что материал не является для них пищей, да и выбирают такое «жилье» лишь тогда, когда другого варианта нет, поскольку они также ограждаются от влаги, пары и прочее.
Технология производства пенополистирола

При изготовлении материала используется вспененный гранулированный полистирол. На многих предприятиях используется импортное сырье (например, поставки сырья из Нидерландов). Также немного (не больше пяти процентов) добавляются другие соединения, повышающие устойчивость к воспламенению. Сам производственный процесс состоит из нескольких этапов, о которых мы намерены поговорить ниже. Безусловно, нельзя сказать, что технология производства является чем-то сложным, но организовать выпуск пенополистирола в домашних условиях без соответствующего оборудования невозможно.
Первый этап: допроизводственное вспенивание
На этапе вспенивания гранулы обрабатываются насыщенным паром при девяноста пяти градусах (как минимум) до тех пор, пока их плотность не достигнет 35 килограмм на кубический метр. Есть специальное устройство для вспенивания. На первых порах процесса гранулы резко расширяются, теряя при этом плотность с высокой скоростью примерно в два раза. Очевидно, что наибольшую активность процедура вспенивания демонстрирует именно в первые несколько минут.
При последующей обработке плотность уже снижается медленнее. Собственно, это и объясняет тот факт, что идеальным временем для такого вспенивания являются именно первые пять-десять минут. Это может регулироваться двумя способами:
— корректированием угла лопастей;
— изменением скорости поступления материала.
Второй этап: повторное вспенивание

Далее происходит еще одно вспенивание гранул. Цель этого процесса – снижение плотности до 15 килограмм на метр кубический.
Третий этап: сушка
Как можно догадаться из названия, далее следует сушка сырья. Это нужно для того, чтобы вода, появившаяся на гранулах после вспенивания, была удалена.
Четвертый этап: гранулы «вылеживаются» на свежем воздухе

Далее гранулам необходимо вылежаться, дабы давление атмосферное сравнялось с давлением внутри них. Когда гранулы остывают, в них образуется вакуум, что открывает путь для поступления атмосферного воздуха внутрь гранул. Отдельно стоит отметить, что это наиболее важный этап, именно тут гранулы пенополистирола получают свои звуко и теплоизолирующие свойства, которые являются самым ценным в готовом материале.
Пятый этап: формировка

При формировке гранулы необходимо склеить между собой, образуя при этом своеобразные блоки необходимых размеров. Существуют специальные прессы, в которые загружается сырье на период от 15 до 180 секунд. Сырье там обрабатывается специальным паром, давление которого должно быть в пределах от 0.7 до 1.5 килограмм на метр кубический. Далее материал остывает не менее сорока минут, после чего аккуратно извлекается из емкостей. Чем больше времени он будет остывать, тем большая плотность у него будет. Подробнее о производстве продукта читайте по ссылке http://www.bazar.kharkov.ua/shop/CID_50.html.
Внутренняя поверхность емкостей для пресса обрабатывается специальной смазкой, которая состоит из следующих компонентов:
1. Хозяйственное мыло и тальк, каждого по двадцать пять грамм на один литр воды.
2. Кремн.-орг. жидкость, пятипроцентная.
3. 3% хозяйственное мыло.
Благодаря этой смеси гранулы не будут приклеиваться к поверхности при обработке.
Шестой этап, он же завершающий: порезка
При порезке получают листы пенополистирола необходимых размеров. Резка может быть вертикальной, горизонтальной и даже фигурной (для этого применяются специальные компьютеры).
В помещении, где производится материал, температура должна быть не ниже восемнадцати градусов тепла.
Изделия из пенополистирола

Все изделия, производимые с использованием данного материала, делятся на группы. Вот они:Изделия военной промышленности. Пенолистирол используется в качестве амортизаторов в тактических шлемах, а также в качестве утеплителя.
В дорожно-строительных работах для того, чтобы утеплить дорожное полотно от промерзания, возведении искусственных возвышенностей, прокладке дорог на слабых типах почвы и так далее.
До недавних пор из него делали теплоизоляторы для холодильников, но в последнее время его заменил полиуретан.С помощью пенополистирола утепляют фасады, а также изготавливают ограждающие конструкции.
Наконец, с его помощью производят одноразовую посуду, специальные упаковки для замороженных продуктов
stroy-dom.info
Технология производства пенополистирола из вспенивающегося полистирола.
Технология производства пенополистирола из вспенивающегося полистирола
1. Физико-химическая последовательность процесса.
Процесс производства пенопласта из вспенивающегося полистирола складывается из четырех последовательных технологических операций.
А. Первоначального производства гранул из вспенивающегося полистиролаБ. Выдержки по времени вспененных гранул из вспенивающегося полистиролаВ. Формирование блоков из вспенивающегося полистиролаГ. Сушка и выдержка по времени блоков из вспенивающегося полистирола.
А. Процесс производства гранул, происходящий во вспенивателе с помощью водяного пара, происходит при температуре 80-100 градусов Цельсия. Благодаря содержащемуся в гранулах порофору (обычно пентан, изопентан или пентан-изопентановая фракция), повышенной температуре и расширению водяного пара, гранулы многократно увеличивают свой объем и принимают микроячеистую структуру.
Б. Во время выдержки по времени вспененных гранул из полистирола происходит процесс диффузии воздуха вовнутрь микро ячеек и выравнивание давления внутри ячеек и атмосферным давлением.
В. Процесс формирования блоков из вспенивающегося полистирола, происходящий в закрытых формах, заключается в нагревании водяным паром вспененных и выдержанных гранул. Благодаря повышению температуры, а также заключенному в порах гранул порофору, воздуху и водяному пару, наступает дальнейшее расширение объема гранул и их взаимное слипание, приводящее к возникновению монолитного блока из пенополистирола. После охлаждения блока в форме наступает ее разъединение.
Г. Процесс выдержки по времени блоков из пенополистирола заключается в двусторонней диффузии воздуха внутрь микропор, и выравнивание давления между внутренним объемом ячеек и атмосферой. Сушка блоков заключается в выпаривании поверхностной влаги в атмосферу.Разрезание блоков из пенополистирола производится с помощью натянутой нагретой проволоки. Кроме того, возможно применение для разрезания блоков продольных и поперечных пил, предназначенных для работы по дереву.
2. Сырье
Сырьем для производства блоков из пенополистирола являются гранулы полистирола, содержащие порофор. В состав порофора входят низкокипящие углеводороды – изопентан, пентан и другие.
2.2 Физико-химические свойства и требования к качеству сырья
Гранулы полистирола, предназначенные для производства блоков и плит, должны иметь вид круглых шариков белого или полупрозрачного цвета. Допускается наличие серповидных и рисообразных гранул полистирола.
Требования к гранулам
Требования | Значение |
Удельная плотность собственно гранул, г/см3 | 1.03-1.05 |
Удельная плотность гранул надіп’ю, г/см3 | Около 0,6 |
Содержание мономера стирола, %, не более | 1,2 |
Вязкость 1% раствора бензина в кПа | 1,0-1,3 |
Максимальное содержание влаги, % | 5,0 |
Просев – максимальный остаток на сите с квадратным сечением ячейки 0,4 мм в % | 4,0 |
2.3. Доставка и хранение сырья.
2.3.1. Требования к доставке сырья
Сырье доставляется в виде упаковок в закрытых средствах доставки – железнодорожным или автомобильным транспортом. Разгрузка производится на разгрузочной рампе и сырьё доставляется на закрытый склад. Контроль за количественными характеристиками доставленного сырья производится лабораторным отделом.
Контроль должен производиться следующим образом:
а) Контроль содержания влажности в гранулахб) Определение содержания мономера в гранулахв) Определение вязкости гранул в 1% бензиновом растворег) Пробное вспенивание гранулд) Определение удельного веса вспененных грануле) Анализ остатка на ситеж) Пробное формование вспененных гранул
Могут быть выполнены дополнительные испытания качества в соответствии с методикой аттестации сырья, поданной производителем или методикой, принятой в стране.
2.3.2. Складирование сырья
Сырье храниться на складе. Температура в складском помещении не должна превышать 25-ти градусов Цельсия. Упаковки должны храниться на деревянных поддонах с высотой штабеля не более 3 м. Металлические бочки складировать в высоту не более 1-3. В складе надлежит обеспечить хорошую вентиляцию.
3. Характеристика источников энергии
3.1. Водяной пар
Процесс производства пенопласта из вспенивающегося полистирола требует доставки тепла как средства энергии нагрева для первичного процесса вспенивания, процесса формирования блоков, а также нагревания воздуха сушилки и пневматического транспортирования вспененного сырья. После проведения эксперимента с другими формами энергии, мы пришли к выводу, что наиболее практичный источник энергии – это водяной пар. Водяной пар, применяемый для преобразования пенополистирола, должен быть насыщенным паром при давлении как минимум 0,25 мПа, не перенасыщенным водой. Оптимальное давление для формирования блоков и последующего вспенивания составляет 0,02-0,07 мПа. Более высокое давление приводит к увеличению скорости поступления пара в форму (время формирования около 20 секунд). Параметры пара определяются при помощи термометра и манометра, установленных на линии подачи и вывода водяного пара. В целях выравнивания давления и равномерного высвобождения пара может быть установлен аккумулирующий сборник.
3.2. Электроэнергия
Электроэнергия применяется для приведения в действие вспенивателя, форм, оснащения для разрезания блоков, пневмотранспорта и установленного освещения. Электроэнергия поставляется от промышленных источников питания при напряжении 380 или 220 В переменного тока. Контроль и изоляция токонесущих частей производится в соответствии с требованиями службы электробезопасности предприятия.
3.3. Сжатый воздух
Сжатый воздух предназначен для приведения в действие пневматических устройств: закрывания и открывания форм, а также выталкивания сформированных блоков. Давление сжатого воздуха от источника должно составлять не менее 5 атмосфер. Полученный сжатый воздух проходит через нагревательный элемент и распределяется при помощи системы трубопроводов. Контроль и обслуживание частей системы подачи сжатого воздуха производит служба энергобезопасности предприятия.
4. Характеристика полуфабриката
Полуфабрикатом для производства блоков из вспенивающегося полистирола являются вспененные гранулы. Они получаются на этапе вспенивания и после высушивания подаются для формирования блоков.
4.1. Физико-химические свойства
Требования | Значение | Место проведения контроля |
Удельный вес насыпью в гр./1 | 15-20 | Обслуживающая лаборатория |
Максимальный диаметр гранул в мм | 20 |
|
Минимальный диаметр гранул в мм | 0,7 |
|
Максимальное время выдержки по времени от момента вспенивания до момента переработки в блоки, в сутках | 5 | Персонал, обслуживающий бункеры накопления |
Максимальное время выдержки по времени от момента вспенивания до момента переработки в блоки, в часах | 8 | Персонал, обслуживающий бункеры накопления |
Наличие агломератов размером более 4 см (вспененных гранул) | не допускается | Персонал, обслуживающий вспениватели |
Максимальное количество выкрошившихся отходов в % | 5 | Персонал, обслуживающий бункеры накопления |
4.2. Доставка и складирование
Вспененные гранулы подаются при помощи пневмотранспорта в бункеры накопления, в которых происходит их выдержка по времени. Температура при выдержке гранул составляет 25-30°С. Время выдержки гранул составляет от 8 часов до 5 суток. Выдержанные гранулы вместе с крошкой отходов пневмотранспортом поступают в дозаторы, находящиеся над формами.
5. Характеристика продукта
Готовым продуктом являются блоки из пенополистирола. Далее их режут на плиты по размерам, зависящим от требований заказчика, что является уже только преобразованием готового изделия, не изменяющим его свойства.
5.1. Физико-химические свойства блоков из пенополистирола
Требования | Значения |
Удельный вес, кг/м3 | 15-20 |
Сопротивление сжатию, при деформации пробки на 10%, более кг/см3 | 0,4 |
Термостойкость, более, °С | 60 |
Сопротивление пропусканию тепла, в ккал/м °С в час | 0,035 |
Отсутствие разбухания в воде в течение 24 часов, менее, в % от объема | 1,5 |
Гигроскопичность в течение 120 часов, менее, в % | 0,6 |
Размеры | Соответствуют требованиям заказчика |
6. Отходы
Максимальное количество отходов, образующихся в цикле производства изделий вспенивающегося полистирола, составляет не более 6,5%. Отходы складываются из выбракованных блоков, получающихся во время формирования и крошки, образующейся при разрезании блоков на плиты. Отходы размельчаются в дробилке (мельнице) и в качестве крошки отходов возвращаются в производство. Крошка в смеси с выдержанными гранулами применяется для повторного производства блоков. Максимальное количество крошки при производстве и формировании блоков не должно превышать 5%.
7. Описание технологического процесса
7.1. Общее описание процесса
7.1.1. Процесс вспенивания гранул
Первой технологической операцией по производству изделий из вспенивающегося полистирола является вспенивание гранул. Процесс вспенивания происходит благодаря расширению пор гранул. Во время вспенивания, производимого во вспенивателе насыщенным водяным паром при температуре 90-100°С, в структуре полистирола образуются микропоры. Водяной пар, подающийся во вспениватель, играет двойную роль – нагревателя и дополнительной причины вспенивания (благодаря быстрой диффузии через стенки микропор), и приводит к многократному увеличению (до 50 раз) объема гранул. Во время вспенивания гранулы размешиваются с помощью механического размешивателя с целью избегания их слипания. Водяной пар подается по системе трубопроводов, подключенной к задней части вспенивателя. Во вспенивателе гранулы размешиваются вертикальным размешивателем, состоящим из системы лопастей, предотвращающих слипание гранул. Расширенные гранулы перемещаются к горловине вспенивателя и высыпаются через засыпное отверстие, размещенное в верхней части стенки вспенивателя. Из вспенивателя гранулы полистирола выпадают в сушилку. Поток теплого воздуха высушивает их и выдувает к горловине инжектора системы пневмотранспорта, которая доставляет гранулы в бункер. Сушилка и система пневмотранспорта обеспечиваются теплым воздухом (более 50°С) путем нагнетания вентиляторами и нагрева паром. В целях обеспечения возможности регулирования количества поданных гранул, предусмотрена регулировка количества оборотов червячного дозатора, давления подводимого водяного пара. Определение количества подаваемых гранул возложено на персонал, обслуживающий вспениватели, которые наблюдают за внешним видом гранул. Контрольно-измерительное оснащение вспенивателя состоит из регулирующих вентилей и контрольного манометра измерения давления водяного пара на линии подачи пара во вспениватель, а также весов для определения веса насыпанных вспененных гранул.Остановка вспенивателя Каждый раз при остановке вспенивателя необходимо выполнить следующие операции:
- Остановка червячного дозатора.
- Отключение подачи пара.
- Отключение механического размешивателя по остывании.
- Опорожнение вспенивателя от вспененных гранул.
Аварийная остановка вспенивателя (отключение электроэнергии, остановка размешивателя) Требует отключения подачи пара и включение сжатого воздуха для остужения гранул. Несоблюдение этих правил приводит к дальнейшему вспениванию гранул и выходу из строя привода вспенивателя. Возобновление работы при аварийной остановке может наступить после ее опорожнения от находящихся внутри гранул и осмотра вспенивателя.
7.1.2. Выдержка гранул по времени
Опорожняющая часть пневматического транспорта направляет гранулы в бункеры. В бункерах происходит процесс выдержки по времени вспененных гранул. Это простая технологическая операция, имеющая, однако, большое значение для дальнейшего производства и влияющая на качество сформованных изделий. Во время выдержки по времени вспененных гранул в бункерах со свободно поступающим воздухом происходит процесс диффузии воздуха внутрь гранул и выравнивания разницы давления между внутренностью гранул и атмосферой. Длительность процесса в зависимости от количества насыпанных гранул, их размера, температуры воздуха колеблется от нескольких до нескольких десятков часов. Общепризнанным является оптимальное время выдержки в течение 8 часов при комнатной температуре. Время выдержки гранул не следует продлевать более недели вследствие потери пор и ухудшения качества изготовленных изделий из передержанных гранул. В целях уверенности, что температура выдерживания гранул, которая должна соответствовать 22-28°С, в помещении, в котором находятся бункеры, устанавливается нагревательная аппаратура, а для контроля служит настенный термометр. В целях обеспечения выдерживания по времени следует производить записи в соответствующих журналах и опорожнение выполнять в соответствии с табличками на бункерах. Выборка гранул производится из нижней части бункеров в систему пневматического трубопровода по трубам и с помощью потока воздуха транспортируется в соответствующие приспособления над формами. Заполнение приспособлений производится периодически, каждый раз после опорожнения. Из приспособлений вспененные гранулы поступают в формы.
7.1.3. Формирование блоков из вспенивающегося полистирола
Формирование блоков из пенополистирола является наиболее важной операцией в цикле производства изделий из пенопласта. Во время этой операции засыпанные в формы вспененные гранулы дополнительно обрабатываются и слипаются между собой, образуя изделие в соответствие с заданной формой, в которой они находятся. Смыслом этой операции является нагревание гранул, которое приводит к эффекту дальнейшего увеличения их объема. Увеличение объема в замкнутом пространстве формы совместно с повышенной температурой материала приводит к слипанию гранул между собой и заполнению всего объема формы. Применяемый метод производства требует использования насыщенного водяного пара как источника энергии. Водяной пар в процессе формирования, так как и при операции вспенивания, также играет роль образователя пор. Существенным элементом цикла является его начальная фаза - это устранение воздуха, имеющегося в свободном пространстве между гранулами и стенками формы. Это производится выдуванием его струей водяного пара. Но и дополнительная роль водяного пара в процессе формирования чрезвычайно важна. Наличие воздуха снижает скорость нагрева гранул и приводит к ухудшению качества их слипания (так называемое рассыпании блоков) или приводит к образованию в форме свободных пустот, не заполненных гранулами, так называемых каверн. Конечной операцией цикла формирования является охлаждение сформированных блоков. От этой, как кажется, простой операции очень сильно зависит качество блоков, а также удачность цикла формования.
Цикл формования блока состоит из следующих операций:
А. Нагревание формы. Перед наполнением формы гранулами надлежит ее нагреть до температуры 80-90°С (при более высоких температурах гранулы будут слипаться сами по себе по мере их засыпания до подачи водяного пара). Во время нагревания форма должна быть закрыта, а конденсат и избыток поступающего пара должен быть направлен выделенным трубопроводом из здания. Нагревание формы имеет конечной целью избежание увлажнения гранул конденсатом, остающимся на холодной поверхности стенок формы. Поступающий на последующих этапах формирования пар должен только дополнительно нагревать стенки формы.Б. Смазывание поверхности формы. Производится с помощью впрыскивания на внутреннюю поверхность формы раствора мыла или другого средства с целью обеспечения свободного отлипания сформированного блока от формы. Операции можно избежать, если гладкие внутренние стенки форм позволяют лёгкую выемку сформированного блока.В. Наполнение формы. Подготовленная в соответствии с пунктами А и Б форма заполняется гранулами через сборник под давлением. Наполнение формы должно быть полным для обеспечения соответствующего качества изделия.Г. Продувание формы водяным паром. После заполнения формы и ее закрывания с помощью пневматического привода и герметичным замыканием – контрольная лампочка на пульте управления, водяной пар подается в верхние и боковые части стенок формы и выводится (вначале как смесь воздуха и водяного пара) через камеру в нижней части формы в коллектор конденсата и водяного пара при открыто находящемся там вентиле. Давление пара в камерах во время операции должно составлять 0,03-0,05 мПа, время продувки 10-20 сек.Применение более длительного срока продувки нежелательно, так как приводит к ухудшению слипания гранул между собой во внешней и нижней частях формы, а наоборот, сокращение времени продувки приводит к остатку воздуха в форме и образованию пустот.Д. Собственно формирование. После проведения продувки, закрывается вентиль отвода пара и конденсата, а также проводятся дальнейшие операции по формованию. В это время возрастает давление пара в форме до 0,04-0,06 мПа, в том числе и в свободном пространстве между гранулами. Возрастание давления должно достигнуть максимального значения и контролироваться с помощью манометров.Во время формования гранулы разогреваются, дополнительно вспениваются и вспененные полностью занимают объем формы. Находящийся там пар проникает через стенки гранул и приводит к слипанию гранул между собой. Время формования блоков составляет 8-12 секунд.
Е. Выемка сформованных блоков. Сформированные блоки выталкиваются из формы при помощи установленного выталкивателя. Для исправного выполнения этой операции необходимо устранение причин прилипания гранул к стенкам формы, которое достигается путем нанесения средств против прилипания перед загрузкой форм. По мере эксплуатации наступает пассивность по отношению к прилипанию стенок форм и в дальнейшем можно избегать смазки.
Контрольно-измерительная аппаратура форм размещена на пульте управления. Кроме того, на линии подачи пара имеется регулирующий вентиль и манометр, а также вентиль на коллекторе конденсатора и отвода из формы. Во время приостановки работы следует прекратить подачу пара, а также сжатого воздуха и электроэнергии. Время пребывания сформованного блока в форме зависит от сырья и составляет 10-30 минут.
7.1.4. Выдержка блоков по времени
Конечно, технологической операцией является выдержка сформованных блоков по времени, когда наступает проникновение воздуха в блоки, а также его сушение. Выдержку и сушение блоков следует производить при температуре 22-30°С в течение 8 часов.
7.1.5. Разрезание блоков на плиты
Последним действием, которое производится над блоками, является процесс их преобразования в плиты. Он заключается в разрезании блоков при помощи разделительного провода. Разрезанию следует подвергать блоки, выдержанные по времени и высушенные. Разрезание блоков разогретым проводом возможно благодаря тому, что температура разогрева провода выше температуры плавления пенопласта и оставляет за собой литую поверхность, благодаря чему усиливается значение упругости материала. Разрезание блоков на плиты производится на оснащении, состоящем из подвижного стола и стальной рамы с натянутыми проводами. Благодаря легкой системе регулировки расстояния между проводами можно регулировать толщину разрезанных плит в соответствии с требованиями заказчика. Разрезанные плиты из пенопласта измеряют в соответствии с требованиями, принятыми на производстве, упаковываются или доставляются навалом через склад заказчику.
8. Стоки и отходы
8.1. Технологические стоки
Стоки предназначены для стока пара, воды и конденсата из вспенивателей, форм и с места расположения производственных мощностей. Единственная защита стока – это защита от механического занесения гранул.
8.2. Отходы
Отходы, образующиеся в процессе производства блоков, а также механического разрезания блоков на плиты вместе с гранулами, рассыпанными во время транспортировки пневмотранспортом, возвращаются в процесс производства. Количество отходов, образующихся на различных этапах производства не должно превышать 6,5% и это значение составляет разницу между нетто произведенным и брутто примененным. 8.3. Испаряемые газы
Образующиеся в процессе производства газы составляют пар и пентан. Наибольшее количество пентана находится в отводах из впенивателей. Выхлоп убирается вытяжной вентиляцией в атмосферу, где он становится безопасным. На рабочих местах, где установлены вспениватели и имеется максимальная концентрация выхлопа, установленное оборудование должно обеспечивать достаточный отвод газов. Вытяжное вентиляционное оборудование обеспечивает многократную замену воздуха в помещении и не допускает концентрацию пентана, угрожающую пожаром или взрывом.
9. Безопасность и гигиена труда
На всех стадиях производства пенополистирол не является токсичным и нет необходимости применять средства для вредного производства. В производственных помещениях, в которых имеется повышенная влажность (помещения вспенивателей и форм), пол следует выложить деревянным паркетом. Каждое место следует обеспечить общей инструкцией обслуживания, в которой определяется способ работы и соответствующие предписания, утвержденные службой безопасности труда, работы в соответствии с технологической инструкцией работы на данном оборудовании. Персонал к работе может быть допущен только после ознакомления с правилами технологии, эксплуатации, обслуживания и безопасности труда на данном оборудовании. Во время эксплуатации следует обратить внимание на следующие вопросы: А. Оснащение рабочих мест общей инструкцией по обслуживанию Б. Подключить систему сигнализации и защиты от возрастания давления пара В. Проводить обслуживание системы трубопроводов пара и воздуха под давлением Г. Во время подачи пара в формы находиться за пультом управления за защитным экраном Д. Проверять состояние пневмотранспорта Е. Запретить курение в производственных и складских помещениях Ж. Проверять состояние вытяжного оборудования З. Не блокировать путей транспортирования и двери Во всех помещениях следует поместить надписи о запрещении курения, гашения пожара водой оборудования под напряжением, оборудовать помещения средствами пожаротушения. Во время ремонтных работ в качестве местного освещения применять лампы с напряжением 24В.
10. Обеспечение пожарной безопасности
Объект производства относится к третьей категории объектов по пожарной безопасности. Здание относится к классу «С», причем помещение склада сырья должно быть класса «А» и иметь огнеупорные двери. Все помещения должны быть оборудованы гидрантами. Кроме того, все помещения должны быть обеспечены средствами пожарного тушения в количестве не менее: углекислотные огнетушители (по два в каждом помещении), 2 углекислотных агрегата тушения (в помещении бункеров и выдержки блоков), 2 асбестовых тента (по 2 в каждом помещении).
11. Процесс двойного вспенивания гранул из пенополистирола.
Процесс двойного вспенивания гранул применяется для уменьшения расхода сырья, менее 14-15 кг/м3. Процесс заключается в том, что во время первого вспенивания, удельная плотность гранул насыпью находится в пределах 16-18 кг/м3, а после их высушивания проводится повторное вспенивание и удельный вес насыпью составляет 11-12 кг/м3. Гранулы после проведения процесса выдержки предназначаются для формирования изделий с плотностью 12-15 кг/м3. Процесс вспенивания можно проводить многократно и довести плотность до 5-7 кг/м3, однако формование изделий из таких интенсивно вспененных гранул затруднено, так как в них остается небольшое содержание порофора. Также изделия из него характеризуются невысокой стойкостью к механическим воздействиям, когда содержание полимера составляет 0,5-0,7 % от объема, а воздуха соответственно 99,3-99,5% объема. Процесс многократного вспенивания был запатентован еще в 1961 году.
11.1. Теоретическое обоснование процесса двукратного вспенивания.
Из кинетической кривой вспенивания следует, что процесс проходит интенсивно в течение первых 2-3 минут и масса насыпанных гранул уменьшается с 550 до 25-30 кг/м3 или в 18-22 раза, соответственно увеличивается объем, а при более долгом вспенивании процесс затормаживается, даже может иметь место увеличение плотности гранул. Это связано с потерей порофора при вспенивании. Во время нагревания гранул до температуры вспенивания (около 100°С) находящийся в них порофор-пентан (химическая формула С5Н12, температура кипения – 36,5°С) превращается в пар. Его утечка невелика и для поддержания равновесия давления гранулы расширяются. Основные потери происходят по причине увеличения объема, а главное времени вспенивания. В процессе многократного вспенивания гранул порофор разрежается воздухом, проникающим в гранулы в процессе выдержки. Время двойного вспенивания почти совпадает со временем одинарного вспенивания, поэтому потери порофора одинаковы в обоих случаях. Во всех случаях вспенивания существенна роль пара. Он является дополнительным источником вспенивания. Благодаря сильной диффузии он проникает в образующиеся микропоры и приводит в соответствие давление в гранулах с внешним давлением.
11.2. Процесс двойного вспенивания.
Технологический процесс двойного вспенивания выглядит следующим образом: на первом этапе вспенивания, проводящейся в атмосфере водяного пара, надлежит довести удельный вес гранул до 16-18 кг/м3. Условиями получения такой интенсивности вспенивания являются соответствующий подбор скорости их дозирования, времени пребывания во вспенивателе или температуры вспенивания посредством использования смеси пара и воздуха. После первой стадии гранулы высушивают на месте в подвешенном состоянии при как можно более высокой температуре и выдерживают на месте. Расчеты по выдерживанию для 1 ступени: температура 15-25°С, время 3-8 часов. Высушенные гранулы повторно поступают во вспениватель и при помощи пара или смеси его с воздухом вспениваются до достижения удельного веса 11-12 кг/м3. Двукратно вспененные гранулы высушивают подобно 1 ступени и направляют в бункеры, в которых их выдерживают. Расчеты по выдерживанию для 2 ступени: температура 15-25°С, время 5-15 часов. После выдержки гранулы предназначаются для формирования блоков. Условия формирования блоков следует подбирать опытным путем, имея в виду повышенную деформируемость гранул при низком удельном весе на сжатие у сформированных блоков.
11.3. Технология процесса и оснащение
Первое вспенивание Во время этого этапа гранулы должны достичь удельного веса насыпью в пределах 16-18 кг/м3. Для этих целей необходимо подобрать определенные параметры вспенивания. Этого можно достичь посредством:
- уменьшения уровня засыпания во вспениватель, что приводит, однако, к уменьшению производительности
- уменьшение количества подаваемого пара во вспениватель и тем самым уменьшение температуры во вспенивателе
- применение смеси пара и воздуха
- сокращение времени пребывания гранул во вспенивателе посредством увеличения скорости дозирования.
Последний вариант является наиболее приемлемым, потому что не уменьшает производительность вспенивателя. Чтобы количество подаваемого через шнек сырья стало меньше (при полном заполнении шнека) при максимальных оборотах надлежит увеличить количество оборотов шнека путем замены ременной передачи.
11.4. Сушение гранул после первого вспенивания
Процесс сушки проводится в существующих сушилках. Не требуется ее специальная доработка для двойного вспенивания.
11.5. Выдержка гранул после первого вспенивания
Несмотря на то, что гранулы после первого вспенивания имеют более высокий удельный вес, время выдержки гранул сокращается и составляет 3-8 часов. Как известно, время выдержки гранул меньшего диаметра меньше. Температуры выдержки составляют 15-25°С. 11.6. Второе вспенивание Процесс второго вспенивания проводится аналогично первому. Следует подобрать те же параметры:
- скорость дозирования
- температура во вспенивателе
Основными критериями оценки правильности работы вспенивателя является определяемый удельный вес гранул насыпью, а также отсутствие появления пыли по выходу из сушилки. В случае появления пыли из гранул, надлежит уменьшить температуру вспенивания (уменьшить количество подаваемого пара или обогатить смесь воздухом) или увеличить скорость прохождения гранул (дозирование) через вспениватель путем увеличения оборотов подающего червякового шнека. Вспененные повторно гранулы, в связи с их малым удельным весом, более чувствительны к механическим повреждениям во время их транспортировки. Поэтому следует уменьшить скорость транспортировки путем изменения скорости работы вентилятора.
11.7. Выдержка гранул после второго вспенивания
Из сушилки через инжектор гранулы направляются в существующие бункеры, где происходит процесс диффузии воздуха в образовавшиеся микропоры. Оптимальное время выдержки после второй ступени вспенивания составляет несколько часов в зависимости от размера гранул. Температура выдержки должна составлять, как и во время первой выдержки, в пределах 15-25°С. Время выдержки при одинаковом удельном весе зависит от размера гранул.
11.8. Процесс формирования блоков
Процесс формирования блоков при двукратном вспенивании не сильно отличается от обычного процесса. Также следует обеспечить продувку формы, наполненной гранулами. Давление пара во время этой операции должно быть в пределах 0,1-0,2 атмосфер, а время продувки как можно меньшим, в границах нескольких секунд. Расчеты продувки и дальнейшая подача пара должны обеспечивать равномерное нагревание гранул во всем рабочем объеме формы. Давление пара во время формования должно составлять 0,4-0,7 атмосфер в зависимости от качества гранул (удельного веса содержащегося полимера). Время формирования с учетом повышенной чувствительности к механическому воздействию не должно быть большим, потому что это приведет к осыпанию (появлению пыли) блоков, даже во время формирования и далее в процессе охлаждения. Общее время воздействия пара должно составлять 15-40 секунд, время охлаждения 5-10 минут, в зависимости от температуры формования, а также давления пара, конструкции формы и ее герметичности. Данные должны определяться опытным путем с учетом качества сырья, а также удельного веса после второго вспенивания.
12. Описание и порядок эксплуатации вспенивателя, предназначенного для ступенчатого вспенивания пенополистирола
12.1. Описание и порядок эксплуатации
Вспениватель следует устанавливать на твердой ровной поверхности и выравнивать по длине и ширине при помощи уровня. Первой технологической операцией является вспенивание гранул. Процесс вспенивания возможен благодаря порофору, который содержится в гранулах. Во время вспенивания, производимого при помощи водяного пара, подаваемого во вспениватель при температуре 90-100°С (давление пара 0,1 мПа) в монолите полистирола возникает микропористая структура. Водяной пар, подаваемый во вспениватель, играет двойную роль: основную – нагревание и дополнительную – источника вспенивания (благодаря высокой скорости диффузии через стенки микропор), приводит к многократному (до 50 раз) увеличению объема гранул. Во время вспенивания гранулы перемешиваются при помощи механической мешалки с целью предотвращения их слипания. Водяной пар подается во вспениватель при помощи трубопровода к нижней его части. Во вспенивателе гранулы перемешиваются вертикальной мешалкой, состоящей из системы лопастей, предотвращающей слипание гранул. Увеличивающиеся в объеме гранулы перемещаются в верхнюю часть вспенивателя и опускаются через отверстие засыпания, размещенное в верхней части стенки вспенивателя. Из вспенивателя гранулы полистирола выпадают в сушилку. Поток теплого воздуха высушивает их и выдувает в горловину (инжектор) пневмотранспорта, который доставляет их в бункеры. Сушилка и транспортная часть приводится в действие теплым воздухом (более 50°С) при помощи вентиляторов и обогревается паром. В целях возможного регулирования производительности и насыпного веса гранул, вспениватель имеет: А. Возможность двукратного вспенивания, Б. Регулировку скорости оборотов шнековых дозаторов. Определение насыпного веса является обязанность обслуживающего персонала, который проводит внешний осмотр вспененных гранул. Контрольно-измерительное оборудование состоит из вентилей закрывания и манометра контрольного давления водяного пара на линии до вспенивателя, а также винта, регулирующего обороты червячной передачи.
12.2. Требования по безопасности труда
- вспениватель может обслуживаться только персоналом, ознакомленным с принципом его действия и устройством, а также с правилами безопасности труда
- обслуживающий персонал должен соблюдать общие правила безопасности труда, обязательные на предприятии
- рабочее место должно быть надлежащим образом освещено и быть чистым, а работник, обслуживающий вспениватель, должен работать в одежде и обуви, находящейся в надлежащем состоянии
- при манипуляциях с паровым вентилем руки должны быть одеты в рабочие рукавицы
Запрещается:
- открывание дверки главного сборника вспенивателя, а также выполнение внутреннего осмотра сборника во время работы мешалки
- включение двигателей привода при открытых защитных кожухах системы ременной передачи
- манипулирование рукой в контрольном лючке червячной передачи при работающем оборудовании.
12.3. Порядок работ перед началом работы вспенивателя
Перед началом работы вспенивателя необходимо выполнить следующие действия:
- Проверить герметичность системы подачи пара по трубопроводу при давлении 0,1 МПа.
- Убедится в правильности подключения к электросети.
- Проверить состояние защитного кожуха на ременной передаче.
- Мусор, попавший в главный сборник, может повредить мешалку и сетку.
- Мусор, попавший в сборник засыпания гранул, может повредить червячную передачу, подающую гранулы в главный сборник вспенивателя.
12.4. Обслуживание во время работ
- Тщательно закрыть дверки на главном сборнике вспенивателя.
- Осторожно открыть паровой вентиль и нагреть главный сборник в течение 10-15 минут.
- Наполнить главный сборник гранулами при помощи червячной передачи. Во время работы сборник (первая ступень вспенивания) должен заполняться автоматически.
3а. Для заполнения во второй ступени вспенивания наполнить бункер второй ступени вспенивания гранулами, прошедшими через первую ступень при помощи червячной передачи большего диаметра. Бункер второй ступени заполняет себя при помощи вентилятора.
- Включить двигатель мешалки в главном сборнике.
- Включить червячную передачу, подающую гранулы в главный сборник.
- Включить пневмотранспорт, а также сушилку.
- Следить за текущей работой вспенивателя.
12.5. Обслуживание по окончании работ
- Выключить червячную передачу.
- Выключить червячную передачу по опорожнении засыпного сборника.
- Перекрыть подачу пара во вспениватель и подать сжатый воздух в целях охлаждения сборника.
- Выключить двигатель привода мешалки в главном сборнике по охлаждении (примерно через 60 минут).
- Выключить вентилятор, а также сушилку.
- Выключить подачу электроэнергии главным рубильником.
Каждая остановка вспенивателя требует:
- Остановка червячного дозатора.
- Отключение подачи пара.
- Отключение механической мешалки по охлаждении.
- Опорожнение вспенивателя от вспененных гранул через дверки во вспенивателе.
12.6. Порядок действий при аварии (выключение электроэнергии, остановка мешалки)
Требует немедленного отключения подачи пара и включения подачи сжатого воздуха с целью охлаждения гранул. Невыполнение этих правил может привести к слипанию гранул, находящихся внутри в агломерат, что может повредить оборудование привода вспенивателя. Возобновление работы вспенивателя после аварийной остановки может производиться после опорожнения находящихся внутри гранул и осмотра вспенивателя
polistirolbeton.ru
Технология производства экструдированного пенополистирола: изготовление

Экструдированный пенополистирол — однородный синтетический материал. В его прочной микроструктуре распределена масса ячеек, составляющих единое тело.

Экструдированный пенополистирол является однородным материалом-утеплителем, который состоит из нескольких пористых ячеек.
Диаметр ячеек очень мал — примерно одна десятая миллиметра, внутри они полые и абсолютно герметичные, то есть имеют капиллярность, приближенную к нулю. Именно это и делает полистирол уникальным материалом с идеальными характеристиками, такими, как:

Схема пенополистирола в качестве утеплителя.
- Низкая теплопроводность пенополистирола.
- Прочность.
- Легкость.
- Влагостойкость, которая обеспечивается очень низкой степенью водопоглащения.
- Сохранение своих свойств под воздействием очень низких температур.
- Отличные звукоизоляционные показатели пенополистирола.
- Долговечность.
- Высокие гигиенические свойства, которые обеспечиваются стойкостью к образованию плесени, росту и размножению бактерий на поверхности пенополистирола.
Все эти свойства пенополистирола делают его идеальным утеплителем. В этом качестве он и используется уже более 70 лет, являясь лидером продаж в этой сфере строительного рынка. В странах Европы и Соединенных Штатах он уже давно вытеснил применение пенопласта.
В нашей стране пенополистирол также набирает популярность благодаря своим эксплуатационным характеристикам и относительно небольшой цене.
Спрос на экструдированный полистирол в России каждый год увеличивается приблизительно на тридцать процентов. Нашел свое широкое применение экструдированный полистирол и в пищевой промышленности для производства тары для упаковки пищевой продукции. Не сложная технология производства полистирола делает возможным его изготовление на небольших производственных линиях.
Технология производства экструдированного пенополистирола

Производство экструдированного пенополистирола — его вспенивание посредством фреонов.
Поначалу технология производства экструдированного пенополистирола представляла собой его вспенивание посредством фреонов. После многочисленных протестов экологов и проведения исследований, установивших, что фреоны входят в список веществ, применение которых участвует в разрушении озонового слоя Земли, в производстве пенополистирола стали использовать углекислый газ СО² как вспенивающий агент.
В общих чертах процесс изготовления выглядит так:
- В сырье (суспензионный полистирол) вводятся необходимые добавки для обеспечения противопожарных свойств (антипирены), для обеспечения лучшего распределения осветлителя (нуклеаторы), а так же красители или пигменты. Далее производится процесс загрузки.
- Производится предварительное вспенивание и вылеживание вспененных гранул.
- Спекание и формовка.
- Обработка в тянущем устройстве.
- Полотно охлаждается естественным путем, при этом происходит окончательное вспенивание. Иногда на мощных производственных линиях применяется принудительное охлаждение методом перекладывания.
- Процесс стабилизации.
- Обработка поверхности до достижения гладкости поверхностей.
- Процесс нарезки и упаковки пенополистирола.
Вернуться к оглавлению
Поэтапное описание технологии и особенностей производства экструдированного полистирола
Вернуться к оглавлению
Загрузка сырья в бункер вспенивающего устройства

Суспензионный полистирол является сырьем для пенополистирола.
Сырьем для производства пенополистирола является суспензионный полистирол, вес при насыпке которого приблизительно равен 500 г на кубический м объема (после вспенивания увеличивается до 15-100 кг). Каждая партия сырья имеет свое время, необходимое для вспенивания, которое должно строго выдерживаться. При превышении временных границ происходит разрушение гранул. В технологии производства вспененного полистирола учитывается качество сырья.
Сырье поступает на склады производства обычно упакованным в мешки по 25 кг или в так называемых биг-багах — мягких контейнерах большого размера и грузоподъемности, имеющих стропы петли для погрузки. Условия хранения сырья должны быть строго соблюдены. Оно должно храниться на поддонах при температуре от 20-25ºC. Сырье не предназначено для длительного хранения, так как со временем могут меняться временные показатели вспенивания. Технология хранения обычно указывается на упаковке.
Перед загрузкой сырья производится механическое перемешивание гранул полимера с добавками-модификаторами. Каждая из них выполняет свою функцию. Помимо уже перечисленных выше для улучшения однородности и мелкой структуры пор добавляют стабилизаторы-нуклезиаты, антипиреновые добавки для повышения огнестойкости, термостабилизаторы и антиоксиданты для защиты от термоокислительной диструкции, абиотические добавки для исключения плесневения. Возможно введение антистатических и синергических добавок. Технология введения добавок подбирается с учетом марки экструдированного пенополистирола.
Вернуться к оглавлению
Приспособления для загрузки

Гибкие шнеки состоят из мягкой трубы и стальной спирали.
Все современные линии оснащены обеспечивающими высокую пропускную способность приспособлениями для загрузки. Более того, производители предусматривают резервные возможности, если будет необходимо увеличение объемов производства пенополистирола. К устройствам подачи предъявляются высокие требования по надежности и способности транспортировки сырья без его повреждения. Более надежными считаются механические подающие устройства.
- Шнеки жесткие определенного диаметра, к которым подсоединена загружающая воронка. Главные преимуществом шнека считается возможность обеспечения при необходимости транспортировки сырья на большие расстояния (до 10 м). Именно жесткий шнек способен обеспечить максимальную сохранность сырья от механического повреждения.
- Гибкие шнеки. Состоят из мягкой трубы и проталкивающего устройства — стальной спирали. Главное достоинство — способность обеспечить как вертикальную, так и горизонтальную подачи. Работают в прерывистом режиме из-за невозможности синхронизации подачи сырья и наполнения бункера предварительного вспенивания.
- Инжектор для подачи сырья, который вставляется непосредственно в бункер. Оснащен всасывающей трубкой, которая заканчивается штуцером. Для сокращения количества всасываемого с материалом воздуха оснащается регулирующими устройствами. Обеспечивает высокую скорость подачи сырья. Однако это скорее недостаток, чем достоинство, так как повышается вероятность повреждения гранул сырья, а так же из-за попадания воздуха снижается производительность и рентабельность производства.
- Вакуумная подача. Производится посредством воздуходувки, работающей при низком давлении, которое автоматически захлопывает клапан загрузки. Воздух выкачивается через фильтр. Работает по прерывистой схеме. Несмотря на малые диаметры подающего устройства, подача сырья происходит в очень высоком скоростном режиме, так что степень повреждения загружаемого материала очень велика.
Вернуться к оглавлению
Процесс предварительного вспенивание и вылеживание сырья

Процесс вспенивания гранул пенополистирола.
Свободное или предварительное вспенивание гранул происходит в предвспенивателе при температуре от 100-110°С и давлении 16-0,22 кг/см². Он состоит из емкости с отверстиями для подачи пара в днище и активатора для размешивания. В процессе вспенивания при обработке паром сырье увеличивается приблизительно в 30-50 раз. Целостность и замкнутость ячеек при этом не нарушается. Далее гранулы сырья под давлением поднимаются вверх и в окно выгрузки выдавливаются в промежуточный бункер, из которого транспортируются пневмотранспортом (система труб и вентиляторов) в бункер вылеживания. Здесь происходит стабилизация давления в расширившихся при вспенивании гранул. Здесь же происходит частичное замещение вспенивающего агента на воздух. Вспенивающий агент вытесняется, а частицы воздуха занимают их место.Технология контроля над процессом осуществляется вручную при помощи весов и мерных емкостей.
Вернуться к оглавлению
Процесс вторичного вспенивания
После выдержки в бункере вылеживания вспененные гранулы сырья вновь подвергаются термической обработке, еще раз увеличиваются в объеме, а так как этот процесс происходит в замкнутом пространстве, то увеличивающиеся в объеме сферические частицы вынуждены «спекаться», деформируясь в многогранники. Для технологии производства полистиролов имеются сводные таблицы по нормам загрузки и времени вспенивания.Обработка поверхности, нарезка и упаковка экструдированного полистирола

Виды обработанной поверхности экструдированного полистирола.
Далее происходит выравнивание листов пенополистирола для достижения ровной поверхности. Полотно обрезается с боков, сверху и снизу. Получив правильные геометрические линии, его разрезают на листы необходимых размеров. Технология выравнивания и нарезки пенополистирола на современных линиях автоматизирована.
Производится дробление и гранулирование обрезки, после чего она снова поступает в производство.
Для больших производств рентабельным является применение устройства для дополнительного охлаждения листов, которое позволяет сократить время охлаждения путем перекладывания листов пенополистирола устройством карусельного типа. Лист охлаждается очень быстро, приблизительно за минуту.
Упаковываются листы пенополистирола, уложенные стопами, специальной упаковочной пленкой стретч-худ.
Вернуться к оглавлению
Типы установок для производства экструдированного полистирола

Процесс производства экструдированного полистирола.
Можно выделить три типа экструзионных установок, которые используется для изготовления экструдированного пенополистирола:
- Установки с одночервячным единичным агрегатом.
- Установки с двухчервячным двойным агрегатом.
- Тандемные установки с парой последовательно установленных агрегатов.
Экструдер представляет собой закрытую линию с поэтапным нагревом и охлаждением.
Шнеки устройства загружают и перемешивают гранулы сырья. Одночервячные экструдеры и двухчервячные экструдеры имеют сходный принцип действия, однако двухчервячные при своей компактности способны создавать более высокое давление в бункерах, что позволяет снижать температуру, что, в свою очередь, приводит к сокращению времени производственного цикла. Поэтому они более экономичны и рентабельны. Оба вида экструдеров лучше применять в небольших производствах.
Но самыми выгодными для производителя являются тандемные установки. Они наиболее рентабельны на больших, многотоннажных производствах пенополистирола, так как процесс разделен между двумя агрегатами. В одном происходит плавление и насыщение паром, во втором происходит гомогенизация, охлаждение формовка.
1poteply.ru
Технология производства пенопласта (пенополистирола) - ООО "ПК ВикРус"
Содержание:
- Предварительное вспенивание гранул.
- Кондиционирование предварительно вспененных гранул.
- Формование пенополистирольных блоков.
- Кондиционирование пенополистирольных блоков.
- Разрезание пенополистирольных блоков на плиты.
- Использование пенополистирольных отходов.
1. ПРЕДВАРИТЕЛЬНОЕ ВСПЕНИВАНИЕ
1.1. Краткая характеристика сырья
В качестве сырья используется вспениваемый самозатухающий полистирол, содержащий 5-6% смеси пентана и изопентана, являющейся вспенивающим фактором. Эта смесь содержится в гранулах полистирола в растворенном виде.
Сырье имеет вид гранул, получаемых путем суспензионной полимеризации стирола. Оно содержит вещество, снижающее горючесть -антипирен.
После подогрева до температуры 90-100°С, под действием улетучивающегося пентана гранулы увеличивают свой объем (процесс вспенивания) примерно в 30-65 раз. В промышленной практике для вспенивания полистирола используется водяной пар, который проникает также внутрь гранул и способствует действию пентана.
Международное обозначение вспениваемого полистирола: EPS самозатухающий FS.
Хранение:
Хранить исключительно в заводской, плотно закрытой таре или контейнерах, установленных в проветриваемых помещениях или под навесом, далеко от источников тепла и огня. Рекомендуется хранить сырье при температуре, не превышающей 20°С.
Продукт, хранимый при рекомендуемой температуре, следует использовать не позднее 3-6 месяцев с даты исследования продукта, указанной в сертификате качества. Продукт из частично опорожненной или поврежденной тары следует использовать немедленно.
В производственных помещениях можно хранить сырье в количестве, не превышающем его среднесуточный расход.
1.2. Переработка вспениваемого полистирола .
Окончательная плотность готового продукта определена уже на этапе предварительного вспенивания.
Важным показателем является контроль давления при процессе вспенивания, для непрерывных предвспенивателей 0,015-0,03 МПа, для циклических 0,015-0,02 МПа.
Во вспенивателе два способа изменения мнимой плотности продукта:
- путем изменения количества подаваемого сырья;
- путем изменения уровня вспениваемого материала в рабочей камере;
Первый и второй способ оказывают влияние на время нахождения вспениваемого материала в рабочей камере. Третий способ влияет на температуру в камере.
Влияние времени нахождения сырья во вспенивателе на мнимую плотность продукта представлено на рис.1.2.
Если время нахождения сырья во вспенивателе слишком продолжительно, то гранулы начинают усаживаться и плотность растет; при слишком высокой температуре вспененные гранулы могут образовать комки. Оба эти явления могут происходить одновременно. И оказывать непосредственное влияние на качество конечного продукта.
Плотность
Продолжительность предварительного вспенивания
Рис.1.2. Зависимость между мнимой плотностью и продолжительностью вспенивания
С целью получения низкой плотности (< 12 кг/м3) применяют двухступенчатое вспенивание. Двухступенчатое вспенивание проводят с помощью того же самого оборудования, которое используется для одноступенчатого вспенивания, с подачей предварительно вспененного сырья через систему вторичного вспенивания.
С целью достижения оптимальных результатов вспенивания гранулы перед вспениванием второй ступени должны быть насыщены воздухом (процесс кондиционирования).
Предварительно вспененные гранулы поступают в сушилку с кипящим слоем, в которой теплый воздух (темп. примерно 30-40°С) проходит через перфорированное днище сушилки, сушит и продвигает гранулы в направлении выгрузочного вентилятора.
Воздушная струя должна распределяться таким образом, чтобы процесс сушки и перемещения гранул протекал равномерно по всей длине сушилки (регулировка осуществляется с помощью заслонок в воздушных камерах сушилки).
Одним из чрезвычайно важных факторов, оказывающих влияние на вспенивание полистирола, является продолжительность хранения сырья. Чем старше сырье, тем продолжительнее вспенивание и тем труднее достичь требуемой мнимой плотности вспененных гранул. Поэтому срок хранения сырья в герметичной упаковке ограничен до шести месяцев.
1.3. Техническое оснащение узла предварительного вспенивания
a) вспениватель ВП-03
b) система вторичного вспенивания СВВ-1
c) поточная сушилка гранул СС-106
d) выгрузочный вентилятор ВПВ-2,5
2. КОНДИЦИОНИРОВАНИЕ ПРЕДВАРИТЕЛЬНО ВСПЕНЕННЫХ ГРАНУЛ
2.1. Основы процесса кондиционирования гранул
В ходе кондиционирования воздух проникает внутрь вспененных гранул вследствие образовавшегося в них вакуума, а из вспененных гранул в атмосферу выпускается влага в виде пара и пентан, не прореагировавшие остатки процесса полимеризации сырья. Указанный газообмен возможен благодаря газопроницаемости полистироловых оболочек.

Рис.2.1. Гранулы вспениваемого полистирола в процессе кондиционирования
Скорость диффузии воздуха внутрь гранул обусловлена, главным образом, мнимой плотностью, температурой окружающей среды и размером гранул. Целью удаления влаги с поверхности гранул в сушилке с кипящим слоем является получение 100% мнимой поверхности, через которую осуществляется газообмен.
Скорость испарения пентана также зависит от плотности, температуры окружающей среды и размера гранул. Из крупных гранул пентан испаряется медленнее, чем из гранул малого диаметра, что обусловлено соотношением между поверхностью гранулы и ее массой.
2.2. Техническое оснащение узла кондиционирования гранул
Силосы, используемые для кондиционирования вспененных гранул, изготовляются в виде легкой металлической конструкции стеллажного типа с контейнерами из ткани, пропускающей воздух.
При перемещении вспененных гранул с помощью струи воздуха, на поверхности гранул накапливаются сильные электростатические заряды. Поэтому чрезвычайно важно тщательно заземлить все металлические элементы силосов, транспортных трубопроводов и остального оборудования.
2.3. Параметры кондиционирования гранул
Температура окружающей среды в цехе кондиционирования гранул не должна быть ниже 15°С, при более низкой температуре продолжительность кондиционирования увеличивается. В летний период, при температуре свыше 20°С время кондиционирования сокращают, а при более низких температурах — продлевают.
При транспортировке свежих гранул в силосы, их мнимая плотность увеличивается в результате столкновений со стенками трубопровода. Поэтому при установке параметров вспенивания необходимо учитывать увеличение плотности при транспортировке.
3. ФОРМОВАНИЕ ПЕНОПОЛИСТИРОЛЬНЫХ БЛОКОВ
3.1. Характеристика процесса формования
При выработке блоков вспененные гранулы свободно засыпают в камеру формы до ее полного наполнения. Затем в форму подают насыщенный сухой водяной пар под давлением 0,2-0,4 МПа, что приводит к дальнейшему увеличению объема гранул. В связи с тем, что гранулы находятся в закрытой камере, сначала заполняется свободное пространство между ними, а затем гранулы сцепляются друг с другом.
Рис.3.1.1. Пример фазового цикла формования блоков без использования вакуума
1) наполнение 2) продувание 3) запаривание 4) охлаждение 5) расформовка
Рис.3.1.2. Пример фазового цикла формования блоков с использованием вакуума

1) наполнение2) вакуум3) продувание4) запаривание — рост | 5) запаривание — выдержка6) выпуск7) вакуумное охлаждение8) разгрузка |
Важным фактором при запаривании блока является подача в камеру в свободное пространство между гранулами соответствующего количества пара в кратчайшее время. Для этого необходима соответствующая вентиляция (продувание), целью которой является удаление воздуха перед началом процесса запаривания. Недостаточная продолжительность продувания приводит к неоднородной плотности и плохому спеканию блока.
Важно также поддерживать постоянную высокую температуру формы, в противном случае значительно растет расход пара (рис.3.1.3) и пар становится мокрым, что снижает качество сцепления гранул.


3.2. Техническое оснащение узла формования
a) блок форма УЦИП 1030.
b) установка вакуумирования ВУ-3,3 с аккумулятором вакуума АВ-1.
c) система вакуумной загрузки и охлаждения блоков.
d) компрессорная установка СБ4/Ф-500
e) аккумулятор пара ПН-5000
f) котел паровой
4. КОНДИЦИОНИРОВАНИЕ БЛОКОВ
4.1. Краткая характеристика процесса кондиционирования блоков
После окончания процесса формования блоки кондиционируют. Кондиционирование проводится с целью снижения влажности и устранения внутренних напряжений, возникающих при формовании. Кроме того, при этом протекают процессы диффузии газов и выравнивания давления внутри гранул с атмосферным давлением, подобные процессам, происходящим при кондиционировании предварительно вспененных гранул.
В процессе кондиционирования блоков очень важную роль играет очередность их использования, соответствующая очередности формования, то есть при отборе блоков для разрезания следует начинать с самых «старых».
5. РАЗРЕЗАНИЕ ПЕНОПОЛИСТИРОЛОВЫХ БЛОКОВ НА ПЛИТЫ
5.1. Характеристика процесса резки пенополистирола
Разрезание блоков осуществляется с помощью реостатной проволоки, нагретой до соответсвующей температуры.
Все отходы подаются в измельчитель, откуда в измельченном виде пневматически транспортируются на вторичное использование.
5.2. Требования по качеству
Внешний вид
Окраска пенополистироловых плит должна быть такой же, как окраска предварительно вспененных гранул полистирола.
Необходимо проводить выборочную проверку плит — по крайней мере 2 шт. на длине каждого блока.
Если плиты отвечают предъявляемым требованиям, то после укладки в стопки они направляются на упаковку.
Если отклонение от требуемых размеров превышает допустимую величину, то следует еще раз проверить по одной плите на всей длине блока, определить причину, произвести соответствующую корректировку промежутков между отрезками реостатной проволоки.
Проверить таким же образом размеры плит, полученных в результате разрезания следующего блока.
Плиты, которые не отвечают предъявляемым требованиям, направляются на вторичное использование.
6. ИСПОЛЬЗОВАНИЕ ПЕНОПОЛИСТИРОЛЬНЫХ ОТХОДОВ
Отходы используется вторично в производстве блоков.
6.1. Техническое оснащение узла
a) дробилка пенополистирольных отходов
b) технологический силос
6.2. Система измельчения
Устройство предназначено для измельчения пенополистироловых отходов, в результате чего получают крошку, используемую в качестве добавки к гранулам полистирола при производстве пенополистироловых блоков. Размеры получаемой таким образом крошки составляют до 15 мм.
Интересно? Оставьте закладку, что бы вернуться сюда позже!
penoceh.com
Технология производства пенопласта | Delo1
Пенопласт полистирольный ГОСТ 15588-86 (скачать 102К)
Пенополистирол - белое однородное вещество, имеющее структуру из склеенных между собой шариков, упругое на ощупь, не имеет запаха, является отличным тепло - звуко изолятором. ПЕНОПОЛИСТИРОЛ - экологически чистый, нетоксичный, тепло- и звукоизоляционный материал, применяемый в строительстве на протяжении уже более 60 лет. Пенополистирол является нейтральным материалом, не выделяющим никаких вредных для человека и его окружения веществ, не подвержен разложению под воздействием микроорганизмов и не имеет ограниченного срока годности (100 лет минимум).
Пенополистирол производят в огнестойком (самозатухающем) исполнении.
Горючесть пенополистирола по ГОСТ 15588-86 | |
1. Начало процесса усадки пенополистирола | 85 - 90°C |
2. Начало плавления | 240°C |
3. Начало процесса термодеструкции пенополистирола с выделением газообразных продуктов | 280-290°C |
4. Температура возможного воспламенения пенополистирола | 360-380°C |
Влага не влияет на теплоизолирующие свойства этого материала и не вызывает образование в нем бактерий и плесени, что позволяет широко использовать пенополистирол также и в пищевой промышленности.
Пенополистирол отлично переносит присутствие асфальтовых эмульсий, рубероида с асфальтовым покрытием, цемента, гипса, извести, воды и всякого рода грунтовых вод. Температура окружающей среды не оказывает отрицательного влияния на физические и химические свойства пенополистирола.
Пенополистирол очень хорошо "держит" тепло. Закладка пенополистирола в наружные стены жилых домов позволяет в несколько раз снизить теплопотери. 12 см пенопласта соответствуют по своей теплопроводности: 50см дерева, 180см кирпича, 4м бетона!
Пенопласт (пенополистирол) применяется:
Для тепловой изоляции в качестве среднего слоя ограждающих конструкций при утеплении жилых домов, складов, гаражей, дач, при текущем и капитальном ремонте жилых и производственных зданий и сооружений, при строительстве ангаров, боксов, крытых площадок. Пенополистирол также незаменим при утеплении трубопроводов, овощехранилищ, промышленных холодильниках, транспортных вагонах, автофургонов, для упаковки продукции при транспортировке, для теплоизоляции наклонной кровли.
Технология производства пенопласта разделяется на следующие этапы:
1. Вспенивание (однократное или многократное). Гранулы ПСВ попадая в камеру предвспенивателя, вспениваются (надуваются) превращаясь во всем хорошо знакомые шарики. При многократном вспенивании уже вспененные гранулы подаются еще раз в камеру предвспенивателя, где они еще больше увеличиваются в размере (надуваются). Многократное вспенивание нужно, если Вам необходимо получить пенопласт низкой плотности. Например, для пенопласта с фактическим весом 12 кг, достаточно однократного вспенивания, а если нужен пенопласт с фактическим весом ниже 12 кг, то потребуется вспенивать гранулы дважды или трижды. Причем перед каждым вторичным вспениванием гранулы должны вылежаться 12 - 24 часа в бункере вылеживания.
2. Вылеживание. После вспенивания гранулы подаются пневмотранспортом в бункер вылеживания. В бункере гранулы должны находиться 12 - 24 часа. За это время происходит стабилизация давления внутри гранул, плюс они попросту высыхают (из камеры предвспенивателя гранулы выходят влажными, а иногда и вовсе мокрыми).
3. Формовка. После бункера вылеживания гранулы засыпаются в блок форму, где под действием пара происходит формовка блока пенопласта. Расширяясь в замкнутом пространстве, шарики пенопласта «склеиваются» между собой образуя монолитный блок.
4. Резка. После того, как блок пенопласта достали из формы его необходимо выдержать не менее суток, перед тем как резать. Это обусловлено тем, что блок пенопласта выходит из блок-формы, как и гранулы из предвспенивателя, влажным, а иногда и просто мокрым. Если же резать мокрый блок пенопласта, то рез получится «рваным» и чрезвычайно неровным. Высушенный блок пенопласта режется по горизонтали или по вертикали на станке для резки пенопласта. Толщина реза пенопласта в среднем 1 мм.
Упрощенная технологическая схема производства пенопласта.
Исходные материалы и ресурсы для производства пенопласта: - полистирол суспензионный вспенивающийся типа ПСВ-С - вода - электроэнергия - пар (парогенератор может быть электрическим, газовым или дизельным)
Схема химических процессов производства пенополистирола | ||
Производство пенопласта - безотходное: весь некондиционный материал дробится и добавляется к предварительно вспененному полистирольному грануляту перед формованием его в блоки пенопласта в количестве 5-10% от свежего сырья.
Для лучшего представления о технологии производства пенополистирола Вы можете посмотреть видео ролик.
www.delo1.ru
Технология производства пенопласта: метод вспенивания гранул полистирола
Производство пенопласта
Пенопласт, или пенополистирол, — экологически чистый, практически безвредный материал. Одноразовую посуду и различные виды упаковки для длительного хранения продуктов изготавливают именно из пенополистирола. Пенопласт — один из самых качественных теплоизолирующих материалов. По соотношению цены и качества этот материал лучше прочих строительных изоляционных материалов.
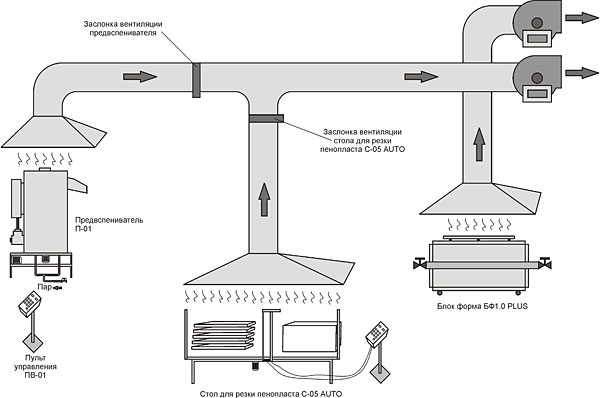
Производство пенопласта.
Толщина стен, в равной степени препятствующих потерям тепла, будет разной у разных материалов. Например, толщина стены из железобетона должна быть 430 см, из кирпича — 220 см, из минеральной ваты — 20 см, а из полистирольного пенопласта — 15 см. Используя пенопласт, можно уменьшить конструктивную толщину перегородок и увеличить общую полезную площадь внутреннего помещения.
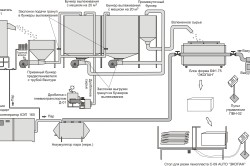
Производство пенопласта.
Использование пенопласта в строительстве позволит уменьшить затраты на отопление. Технические характеристики пенополистирола стабильны во времени, он влагостойкий и сохраняет свои параметры при пониженных температурах. У пенопласта высокая прочность к механическим воздействиям. Что немаловажно, он устойчив к возгоранию и имеет первую степень огнестойкости.
При горении пенопласт разлагается на воду и углекислый газ, а они, в свою очередь, не позволяют пламени распространиться. Влагостойкость этого материала позволяет использовать его для утепления цокольных этажей, стен подвалов, фундаментов и других подземных элементов зданий. Пенополистирол не создает питательную среду для бактерий и грибков, не выделяет растворяющихся в воде веществ и не разлагается. Какова же технология производства пенопласта?
Методы изготовления пенопласта
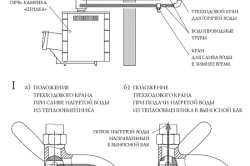
Упрощенная технологическая схема производства плит из пенополистирола: 1. Предвспениватель. 2. Бункер промежуточной выдержки вспененных гранул. 3. Бункер вторичного сырья. 4. Вентилятор системы пневмотранспорта. 5. Мельница-дробилка вторичного сырья. 6. Дозатор-смеситель. 7. Блок-форма. 8. Гидростанция с постом управления. 9. Резательный стол. 10. Склад готовой продукции.
Первый метод изготовления пенопласта был разработан в 1951 году германской фирмой «BASF». Простота аппаратурного обеспечения и технологической схемы позволила методу распространиться во всех развитых странах мира. Из отдельных вспененных гранул можно изготовить модели довольно сложной конфигурации, из большого блока этого сделать невозможно.
Раздельные гранулы можно вспенить в 6-7 раз быстрее, чем большой блок; при вспенивании цельного блока полистирола слои на поверхности подвержены воздействию тепла более продолжительное время, чем внутренние слои, что может привести к разрыву стенок ячеек и нарушению структуры поверхностных слоев материала.
Сырьем для изготовления пенопласта является полистирол в виде суспензии. Суспензионный полистирол еще называют бисерным. Его получают методом полимеризации стирола с добавлением изопентана. Сейчас выпускают суспензионный полистирол с пониженным уровнем горючести, иначе говоря, затухающий самостоятельно.
Горючесть полистирола, и, как следствие, пенопласта снижается введением в его состав антипирена или тетрабромпараксилола. Основные свойства гранул пенополистирола определяются весом молекул и содержанием в них стирола, не вступившего в реакцию полимеризации. Метрический состав гранул и влияет на объемный вес материала. Полистирол, применяемый для вспенивания, должен соответствовать республиканским техническим условиям 6-05-959 и 6-05-1019 от 1966 года.
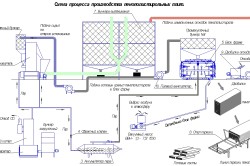
Схема процесса производства пенополистирольных плит.
Величина гранул у суспензионного полистирола техническими условиями определена в пределах от 0,6 мм до 3,2 мм. Молекулярный вес полистирола должен быть от 35000 до 45000. При большем молекулярном весе гранулы недостаточно вспениваются от повышенной температуры размягчения, а при меньшем весе — слипаются на стадии предварительного вспенивания.
Суть процесса изготовления пенопласта состоит в том, что при нагреве выше 80°С полистирол из стеклообразного состояния переходит в текуче-вязкое состояние. А изопентан, в свою очередь, при температуре выше 30°С вскипает и вспенивает гранулу полистирола.
Такая технология производства пенополистирола возможна благодаря способности гранул полистирола свариваться между собой при воздействии относительно небольших температур (до 100°С) и воды.
Технология производства пенополистирола состоит из таких операций:
- предварительное или первичное вспенивание гранул;
- при необходимости сушка ранее вспененных гранул;
- выдержка и последующее формование, спекание изделий;
- охлаждение формованных изделий и блоков;
- резка на изделия или блоки необходимых размеров;
Основная особенность данной технологии изготовления пенополистирола — это то, что вспенивание гранул состоит из 2-х стадий.
Стадия первичного вспенивания
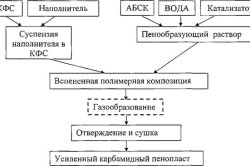
Схема получения карбамидного пенопласта усиленного.
На стадии первичного вспенивания в гранулах появляются ячейки, равномерно распределенные и заполненные парами, они имеют форму многогранников. Толщина стенки ячейки не более 0,005 мм. Размер ячеек около 0,15 мм. Молекулы полистирола в стенках ячеек находятся в строго ориентированном состоянии, и это повышает устойчивость вспененных гранул. Процесс первичного вспенивания довольно трудоемкий. Необходимо обеспечить абсолютное заполнение объема формы, чтобы пенопласт обладал определенным объемным весом. Это зависит от продолжительности вспенивания, температуры процесса, гранулометрического состава и молекулярного веса.
Гранулы полистирола, из которого делают пенопласт, имеют плотность 500-550 кг/м³. После предварительного вспенивания их плотность составляет 15-50 кг/м³. Каждая партия полистирола вспенивается при определенной оптимальной температуре. Оптимальная температура устанавливается для баланса внешнего давления и давления внутри гранул. Увеличение времени вспенивания приводит к увеличению объемного веса, созданию пористой структуры и, как следствие, разрушению гранул.
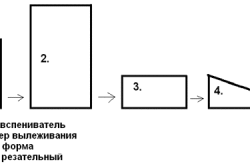
Оборудование для производства пенопласта.
Расширение гранул происходит только в начале стадии первичного вспенивания, а затем диффузия паров воды оказывает большее влияние. Водяные пары проникают через стенки гранул полистирола. При значительном повышении температуры проницаемость стенок гранул несколько снижается, но остается значительной. В сравнении с диффузией паров проникновение паров в середину ячеек довольно интенсивно.
Предварительное вспенивание проводится с целью снижения количества изопентана, вводимого в состав полистирола. Для того чтобы создать необходимое давление газа и получить изделие с объемным весом в 25-30 кг/м³, нужно 12-15% изопентана. Однако в гранулах полистирола изопентана содержится всего 4,5-5%. При формовании пенопласта нужное давление достигается путем выдерживания сухих гранул. Атмосферный воздух после предварительного вспенивания засасывается внутрь гранул, где образовался вакуум при конденсации.
Предварительное вспенивание проводят с помощью пара, горячей воды или токов высокой частоты. Полистирол нагревают до температуры 100-120°С. Объем гранул при этом увеличивается в 40-50 раз. Зависит это от свойств исходного материала. Для этой процедуры используют различные вспениватели гранул пенополистирола непрерывного или периодического действия.
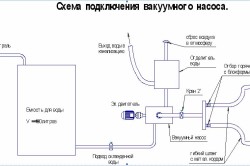
Схема подключения вакуумного насоса.
При небольших объемах производства рационально использовать вспениватели периодического действия, со средой воздействия в виде воды или пара. В случае вспенивания посредством горячего воздуха нет необходимости сушить и выдерживать гранулы. Однако снижение коэффициента теплопередачи сказывается на эффективности и приводит с неравномерному вспениванию отдельных гранул.
При производстве пенополистирола в больших объемах выгоднее использовать водяной пар. В этом случае можно автоматизировать предварительное вспенивание. Гранулы увлажнятся незначительно, отпадет необходимость сушки. В настоящее время такой метод наиболее распространен. При помощи токов высокой частоты этот процесс значительно ускоряется.
Формование изделия
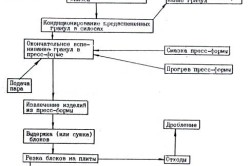
Технологическая схема производства теплоизоляционных плит из полистирольного пенопласта.
Для того чтобы осуществить формование, необходимо наполнить форму гранулами на 65-70% объема. При повторном нагревании полистирол снова размягчится и станет вязким и текучим. В ячейках гранул создастся избыточное давление паров, воды и воздуха. Результатом этого будет их увеличение. Гранулы пенополистирола уплотняются, деформируются и превращаются в многогранники.
В тех местах, где они соприкасаются, происходит сваривание и образуется прочное монолитное изделие. В процессе вторичного вспенивания на все стенки формы оказывается определенное давление. Величина этого давления напрямую зависит от плотности пенопласта. При достижении максимального давления фиксируется момент окончательного формования. Своевременная остановка процесса формования сильно влияет на качество пенополистирола.
Если затянуть процесс формования, ячейки гранул могут разрушиться и возникнут усадочные явления. В случае преждевременного окончания процесса вторичного вспенивания гранулы плохо сплавляются, ввиду недостаточного нагрева. И в первом, и во втором случае, это скажется на механических показателях и качестве изделия.
teplomonster.ru
Технология производства полистирольного пенопласта -
Полистирольный пенопласт является эффективным теплоизоляционным материалом. По сравнению с другими утеплителями он обладает наилучшим сочетанием исключительно малого объемного веса, хороших тепло- и звукоизоляционных свойств, достаточной жесткости и весьма незначительного водопоглощения.
Объемный вес пенопласта 20—40 кг/м3. Это — в 25—30 раз ниже показателей наиболее эффективных ячеистых бетонов. Коэффициент теплопроводности пенопласта 0,027—0,03 ккал/м час град, т. е. при толщине в 1 см он обладает такой же теплоизоляционной способностью, как стена из кирпича в 20 см. Водопоглошение при длительном пребывании в воде не превышает 3—5%. Прочность при сжатии 0.5—1,5 кг/см2.
Пользуясь таким утеплителем, можно снизить вес 1 м2 стеновой панели до 8—10 кг.
Разработанный в Ленинградском научно-исследовательском институте полимеризационных пластиков исходный полуфабрикат, предназначенный для изготовления пенопластовых изделий беспрессовым методом, представляет собой суспензионный (бисерный) полистирол, в гранулы которого в процессе полимеризации введен типа изопентана. Находясь в полистироле в твердом растворе в количестве около 3°т хорошо удерживается в нем даже при температуре несколько выше точки кипения ( 28°) при стеклообразном состоянии полимера, не изменяя удельного веса (плотности) последнего.
При температуре -f-80° и выше полистирол переходит из стеклообразного в высокоэластичное состояние, значительно размягчаясь по мере повышения температуры.
Равномерно распределенный в массе полистирола изопентан переходит при нагреве свыше 28° в газообразное состояние, вспенивает размягченные (при +80° и выше) гранулы потистирола и увеличивает их объем в 10—12 раз.
При этом газообразный изопентан концентрируется в полистироле в замкнутых ячейках, имеющих вид округлых многогранников размером от 0.1 до 0.7 мм с тонкими перегородками между ячейками.
Скорость вспенивания и увеличение объема гранул зависят от температуры нагрева их. т. е. от соотношения между внутренним давлением газообразного изопентана и вязкостью размягченного полистирола.

Быстрое вспенивание полистирола начинается при 95—98°. Более энергично оно протекает при прогреве гранул пароводяной смесью, горячей водой (наиболее теплоемким теплоносителем) и значительно медленнее протекает при прогреве гранул горячим воздухом.
При вспенивании полистирола в закрытой форме его гранулы, увеличиваясь в объеме, заполняют полость формы, а затем уплотняясь сплавляются между собой, образуя пенополистирольное изделие.
Возможность получения изделий того или иного объемного веса из суспензионного полистирола с введенным в него изопентаном определяется следующим расчетом:
плотность полистирола = 1,05 г/см3
молекулярный вес изопентана (С5Н12) =72 грамм изопентана при 760 мм рт. ст. и температуре 30° занимает объем 310 см3, при температуре 100° — 390 см3, при 110° — 400 см3.
Получение изделий с объемным весом до 0,02 г/см3 из предварительно вспененных гранул полистирола с содержанием изопентана 3% объясняется следующим.
Предварительно вспененные гранулы полистирола прн охлаждении до 80° быстро отвердевают и наружная часть их становится жесткой, неспособной при дальнейшем охлаждении свой объем в соответствии со снижением бъема изопентана, особенно при переход, его жидкое состояние (при +28°), когда в ячейках образованных газообразным изопентаном. создается заметное разрежение (вакуум). В связи с этим через тон
кие стенки ячеек в них постепенным влиянием разности давлений проникает которое количество воздуха. Проникший в ячейки вспененного полистирола воздух наполняет их газообразным продуктом, способным при повторном нагреве предварительно вспененных гранул и быстром размягчении полистирола произвести дальнейшее увеличение объема (окончательное вспенивание).
Этим и определяется необходимость предварительного вспенивания при изготовлении изделий с объемным весом 0,02—0,06 г/см. Предварительно вспененные гранулы следует просушивать (или проветривать). Это необходимо для точной дозировки гранул с целью получения изделий заданного объемного веса, а также ввиду практически установленной целесообразности вспенивания гранул до требуемого насыпного веса.
Принципиальная технологическая схема производства полистирольного пенопласта показана на рис. 2.
Доставляемый в цех электрокарами полистирол высыпается из мешков в приемный бункер 4 вентилятора высокого давления 2 и воздухом подается в циклон 6.

Полистнрольнын пенопласт малого объемного веса представляет особый интерес для холодильной техники как теплостойкий изоляционный материал, который не разрушается от гниения и надежен против действия сырости.
На комбинате разработана и практически осуществлена принципиально новая технологическая схема производства полистирольного пенопласта.
Работы велись в содружестве с Ленинградским научно-исследовательским институтом полимеризационных пластиков, Кусковским химическим заводом и специалистами системы Главмоспромстройматериалов.


Заполненная пенополнетиролом форма до роль гангу, установленному под дозирующим устройством, отодвигается, а на ее место, под засыпку пустая форма. Форму с пенополтиролом тельфером устанавливают на запарочную вагонетку; на узкоколейном пути формируется состав m 15 вагонеток, которые лебедкой направляются в автоклав.
Выдержка изделий в автоклаве под давлением 0,8—1,2 атм длится 50— 60 мин. В условиях влажной среды при температуре 103—105° ленополистирол окончательно вспучивается, приобретает форму изделия.
После тепловой обработки изделия должны остывать непосредственно в формах. Откзание до 50—40° производится медленно.
Остывшие изделия распалубливаются и тельфером транспортируются в сушилку. Сушка производится при 30—35° с постоянной циркуляцией воз духа Продолжительность сушки зависит от размера изделий. Влажность их по выходе из автоклава составляет 40%, а после сушки не должна превышать 10%.
Формы после распалубки смазываются и тельфером подаются на рольганг под загрузочное устройство.
Как видно из технологической схемы, для транспортировки сырья применяется пневмотранспорт Пневмоустановка (рис. 3) состоит из вентилятора высокого давления, приемного бункера, воздуховода диаметром 150 мм и длиной 52 м, циклона.
В приемный бункер загружается сырье, которое увлекается затем воздушным потоком, создаваемым вентилятором Количество подаваемого сырья регулируется шибером приемного бункера. Вентилятор высокого давления имеет следующую характеристику: производительность 8 000 м3/час; давление, развиваемое вентилятором, 425 кг/м2; число оборотов электродвигателя 1440 в мин.; мощность его 10 кет; скорость движения воздуха 68 м/сек
Двигаясь по воздуховоду сырье поднимается па высоту 14 м и поступает в циклон Гам частицы сто оседают, а очищенный воздух выбрасывается в атмосферу. Для лучшей очистки воздуха от сырья г, циклоне предусмотрена поворотная сетка. Характеристика циклона- производительность 7 500м3/час диаметр 1 226 мм, высота 4 150 мм размеры входного патрубка 450x250 мм Применение пневмотранспорта обеспечивает полную механизацию подачи сырья без потерь к установкам по вспучиванию пенополистирола. На случай поступления сырья повышенной влажности предусматривается установка калориферов
Для предварительного вспучивания пенополистирола группой инженерно-технических работников комбината спроектирована и изготовлена принципиально новая, непрерывно действующая установка (рис. 4), состоящая из следующих узлов: приемного бункера пенополистирола, шнекового дозатора, трубчатого шнека, паровой рубашки, набора шестерен, редуктора и электродвигателя
Принцип работы установки заключается в еле дующем. В приемный бункер засыпается исходное сырье—полистирол, из бункера оно просыпается в шнековый дозатор, которым беспрерывно подается в трубчатый шнек. Шнек представляет собой трубу диаметром 200 мм, внутри которой вращается лопастный винт, с его помощью полистирол с определенной скоростью продвигается от загрузочного отверстия до выхода (рис. 5).
Наличие двигателя постоянного тока позволяет изменять в широком диапазоне число оборотов лопастного винта, тем самым изменяя скорость прохождения сырья через установку в зависимости от качества сырья.
Весь механизм смонтирован на легкой сварной раме. Установка проста в изготовлении и обслуживании.
Для повторного вспучивания с целью получения изделий из пенополистирола нами используются автоклавы 2x17 м. Это позволяет изготовлять плиты-панели больших габаритов и другие изделия различных конфигураций.
Процесс тепловой обработки пенополистирола при вторичном вспучивании в автоклаве показан на графике (рис. б). Весь процесс от загрузки форм до подачи под следующую загрузку продолжается 2 часа.
Одним из существенных недостатков полистирольного пенопласта является его горючесть. На комбинате проводятся сейчас опыты повышению огнестойкости этого материала. Изделия из пенопласта пропитываются растворами диаммония фосфата и сульфата аммония.
Результаты опытов показали:
1) возможность значительного повышения огнестойкости полистирольного пенопласта. Так, например, кубик пенопласта размером 100Х100Х10О мм, пропитанный указанными растворами, не загорается от непосредственного соприкосновения пламени спички или свечи;
2) после поверхностной пропитки полистирольного пенопласта указанными растворами он не гигроскопичен и не оказывает корродирующего действия на черные металлы и другие материалы, с которыми соприкасается.
Доступность, дешевизна и незначительный расход пропиточных материалов позволяют получать полистирольный пенопласт повышенной огнестойкости.
Недавно на комбинате введена в действие технологическая линия мощностью 30 тыс. м3 пенопласта. Если до сих пор производство пенопласта было организовано в сравнительно небольшом масштабе, по довольно сложной технологической схеме, требующей применения мощного прессового оборудования, что ограничивало габариты получаемых пенопотистирольных плит, то теперь на нашем комбинате практически можно изготовлять плиты и блоки любых размеров и конфигураций, причем беспрессовым методом.


alyos.ru
- Технология производство щебня
- Основа бумага для салфеток
- Чтобы открыть массажный кабинет что нужно
- Технология приготовления домашнего творога
- Изготовление сетки рабицы
- Реальні бізнес ідеї
- Как открыть свое дело в беларуси с нуля
- Производитель бумажные салфетки
- Как открыть сеть отелей
- Производители гипсокартона
- Производство батончиков
© 2005-2018, Национальный Экспертный Совет по Качеству.