Новейшие эффективные технологии и оборудование переработки биомассы. Технология производства топливных брикетов
Технология производства топливных брикетов из древесных отходов
Экотехнологии сегодня осваиваются практически во всех сферах народного хозяйства. Главными принципами стали использование вторсырья, безопасное производство и минимизация ущерба окружающей среде. Одной из таких технологий является производство топливных брикетов из древесных отходов. В основе производства заложен метод прессования древесной муки, которую получают из отходов деревообрабатывающей промышленности.
Производимые брикеты отличаются повышенной плотностью и пониженной влажностью. По температуре горения их можно поставить на одно место с углем, но при этом продукты сгорания содержат меньше вредных веществ, чем натуральная древесина. К тому же топливо оставляет меньше золы, выделяет меньше смол и горит дольше.
Сырье
В качестве сырья в основном применяется древесина, лузга подсолнечника, шелуха риса и гречихи. Могут также использоваться добавки торфа, угольной пыли, соломы и тырсы. От состава брикета зависят такие качества как теплотворная способность, зольность и выделение сажи.
По этим качествам брикеты условно можно разделить по предназначению. Для каминов используется топливо с наименьшей зольностью и выделением сажи, чтобы не засорять дымоход. Твердотопливные котлы менее «капризны», поэтому баланс качеств смещается в пользу теплотворной способности. Для промышленных печей главным параметром является выделение температуры, а остальные качества отходят на второй план. Брикеты также могут использоваться для приготовления пищи на открытом огне, а здесь важна чистота продукта. Для этих целей используют евродрова из лиственной древесины.
Для того чтобы получить брикеты с заданными параметрами, технологи учитывают качества каждого элемента в отдельности и составляют необходимые пропорции.
- Древесина – калорийность 5043 ккал/кг, зольность 0,5-2,5%
- Лузга подсолнечника – 5151 ккал/кг, зольность 2,9-3,6%
- Солома – 4740 ккал/кг, зольность 4,8-7,3%
- Тырса – 4400 ккал/кг, зольность 0,7%
- Шелуха риса и гречихи – 3458 ккал/кг, зольность 20%
Добавки торфа и угольной пыли применяются только для промышленных печей.
Производство
Технология производства брикетов из опилок разделяется на 2 вида ‒ холодного и горячего прессования.
Холодное производство
Холодное прессование больше относится к частному производству и характеризуется малой производительностью, а также более низкой плотностью изделий. Зато такая технология изготовления топливных брикетов из опилок менее затратная и позволяет организовать производство для собственных нужд непосредственно на малом деревообрабатывающем предприятии.
Стружка не нуждается в дополнительном измельчении и просушке. Напротив, перед прессованием ее увлажняют до 40%, а в качестве связующего добавляют 2-3% крахмала. Прессование производится на ручном гидравлическом оборудовании, которое напоминает домкрат. Подготовленная стружка засыпается в цилиндр и сжимается поршнем. Затем брикет просушивается.
Горячее производство
Эта технология является промышленным способом и требует серьезного подхода. Для изготовления брикетов из опилок применяется целый ряд оборудования, включающий дробилки, сушки, измельчители и конвейерные ударные прессователи.
Подготовка сырья
Древесные отходы в составе с другими предусмотренными добавками загружаются в дробильные агрегаты, где дробятся до фракции не более 25 мм. Этот процесс предусмотрен для крупных древесных отходов, если же в качестве сырья применяется стружка, его можно пропустить.
Далее дробленая древесина попадает в барабанные сушилки, где высушивается горячим воздухом до состояния влажности 4%. Технологи отмечают, что этот процесс ‒ один из важных, поэтому влажность должна точно соответствовать параметрам.
После просушки сырье загружается в измельчитель, где доводится до консистенции древесной муки. В таком виде древесина готова к прессованию.
Прессование
Непрерывный процесс прессования производится на специальном оборудовании, выполняющем 20 ударов поршня в секунду. Сила сжатия, в зависимости от вида оборудования, варьирует от 300 до 1400 кгс/см².
При таком сильном сжатии материал нагревается до 200°C. При нагреве древесина выделяет смолы, которые служат естественным связующим, поэтому введение сторонних вяжущих не требуется. Сжатая древесная мука проходит через фильеру, которая формирует брикет.
Нарезка
Из прессовального агрегата брикет выходит сплошным и сразу нарезается. При нарезке автоматически брикеты отделяются и по транспортерной ленте отправляются на остывание и упаковку.
Если опустить брикет в воду, он тонет, что свидетельствует о большой плотности. Для сравнения плотность дуба ‒ 0,81 г/см³, в то время как плотность брикета ‒ 0,8-1,4 г/ см³.
Формат
Брикеты различаются по формату и плотности. Это зависит от оборудования, на котором их прессуют. В зависимости от фильеры – выходной насадки, разделяют 3 вида.
- Пини-кей – имеют четырех или шестигранный формат с продольным круглым отверстием в середине. Отверстие предусмотрено для улучшения качеств горения. Этот вид лидирует по плотности 1,4 г/см³.
- Нестро – имеет сплошное круглое сечение. Некоторые производители специально подрезают грань, чтобы упростить выкладку в камине и евродрова не скатывались. По плотности нестро идут на втором месте 1,15 г/см³.
- Руф – прямоугольный параллелепипед. Формат удобный для топки твердотопливных котлов и печей. Плотность ‒ 0,8 г/см³.
Все 3 вида не отличаются по качеству, составу и массовой теплотворности. Единственный их недостаток ‒ цена, хотя если сравнивать с дровами не в массовом эквиваленте, а в тепловом, то выходит одинаково.
qwizz.ru
Технология производства топливных брикетов из влажного измельченного сырья - - из влажного мелкого сырья
Технология производства топливных брикетов из влажного измельченного сырья
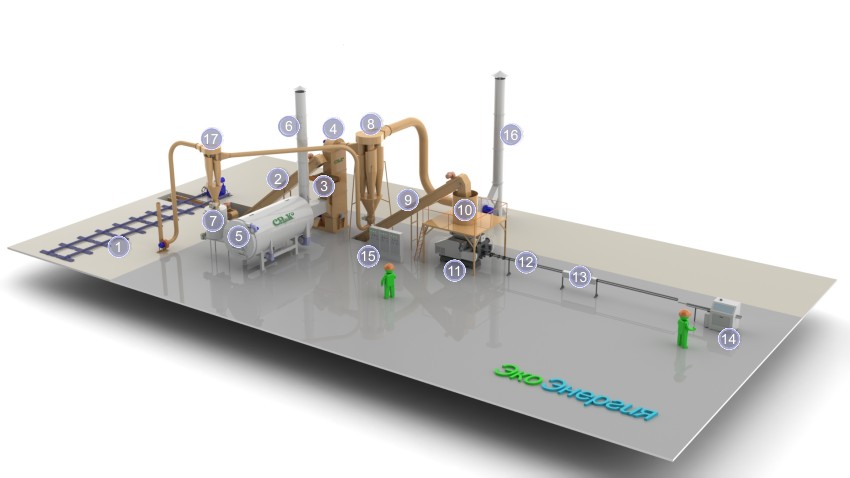
По этой технологии можно производить топливные брикеты из влажных мелких древесных отходов (опилки, стружки, щепа), куриного помета с подстилкой, обезвоженного ила очистных сооружений ЦБК, фрезерного торфа, лигнина, сортированных твердых бытовых отходов (ТБО), навоза (после ферментации) и костры льна.
Характеристики сырья: влажность – до 65%, размер частиц – до 50х25х10 мм.
Сырьё подвозится автотранспортом (либо погрузчиком) и ссыпается на механизированный склад “подвижный пол” (1). Стокеры подвижного пола имеют гидравлический привод и под его действием совершают возвратно-поступательные движения. Лопатки (“крылья”) стокеров имеют клиновидную форму, поэтому при движении стокеров сырье с регулируемой скоростью подачи направляется к цепному (скребковому) транспортеру (2), далее сырье подается на дисковый сепаратор (3). На нем от сырья отделяется камни, коренья и т.п. примеси, которые попадают в переносной контейнер (на схеме не показан), а сырьё через самотёк попадает в загрузочную секцию Агрегата Сушки-измельчения (4). Сюда же подаются продукты горения из теплогенератора (5) (подробнее – в статье «Технология сжигания биомассы») и засасывается холодный атмосферный воздух через аварийно-растопочную трубу (6). Первоначально смешиваются продукты горения и холодный воздух, пропорция смешивания регулируется автоматически, что обеспечивает поддержание заданной температуры теплоносителя. Затем теплоноситель смешивается с влажным сырьем и засасывается в Агрегат Сушки-измельчения (4). В нем сырье измельчается и затем высушивается, поднимаясь в потоке теплоносителя к динамическому классификатору, находящемуся в головной секции Агрегата Сушки-измельчения. Динамический классификатор, частота которого задаётся с пульта управления (15), пропускает мелкое и сухое сырье, а крупные и влажные частицы сырья возвращает к ротору Агрегата, этот процесс повторяется до получения необходимой влажности и степени измельчения сырья (подробнее – в статье «Технология сушки-измельчения»). Измельчённое и высушенное сырьё (с этого момента его принято называть мукой) засасывается в осадочный циклон (8) за счет разряжения, создаваемого дымососом (не виден). В циклоне мука осаждается за счет центробежной силы и двигается вниз, а отработанный теплоноситель выбрасывается в дымовую трубу (16). Из циклона мука через шлюзовой затвор подаётся в шнековый или цепной транспортер (9), далее поступает в бункер брикетного пресса (10). Внутри бункера находится устройство, препятствующее слеживанию муки. Из бункера мука шнековым питателем с регулируемой скоростью подачи направляется в брикетный пресс (11). В прессе мука сначала попадает в камеру (или 2 камеры) предварительного прессования, откуда шнеком (или двумя встречно направленными шнеками) подается в камеру прессования. В камере прессования мука вдавливается подвижным поршнем (пистоном) в коническую неподвижную матрицу, где под действием большого давления происходит формирование непрерывного брикета (далее для простоты – «брикетов»). Брикеты, выходящие из пресса, имеют высокую температуру и непрочны, поэтому они направляются в тоннельный охладитель брикетов (12). В процессе охлаждения влажность брикетов уменьшается за счет испарения влаги, и в них происходят физико-химические изменения. В результате они приобретают необходимую твердость, влажность и температуру. Продвигаясь по туннелю охладителя, который в данном случае является одновременно и транспортером, непрерывный брикет проходит металлодетектор (13) и поступает в автоматическую пилу (14), где происходит его нарезка на брикеты заданной длины. Далее брикеты поступают на участок упаковки и склад готовой продукции (подробнее - в статье "Технологии упаковки").
Теплогенератор в данной схеме может загружаться топливом как в ручном (через дверцу), так и в автоматическом режиме - из бункера топлива (7). Пополнение бункера топлива происходит автоматически за счет возврата части муки от осадочного циклона (8) системой пневмотранспорта (17). Опционально бункер топлива может пополняться дополнительным транспортером с отдельного склада топлива (не показан).
Технологии производства топливных шайб и четвертаков имеют незначительные отличия от технологии производства брикетов. Перейти к описанию технологии производства топливных шайб и четвертаков.
Технология производства топливных брикетов в форме параллелепипедов (кирпичиков) имеет незначительные отличия. Перейти к описанию технологии производства топливных брикетов в гидравлических прессах.
Брикеты
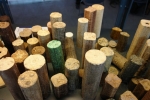
Брикеты - спрессованные частицы растительного происхождения, имеющие форму цилиндров диаметром более 25 мм. (либо имеющие в сечении многоугольник, иногда - с отверстием в центре). Брикеты могут быть изготовлены из древесины, тростника, торфа, куриного помета, лузги, соломы, угольной пыли и многих других видов растительного сырья, а также твёрдых бытовых отходов, макулатуры, использованных автопокрышек. Чтобы получить качественные брикеты, необходимо выполнить 3 основных условия: использовать качественное оборудование, строго соблюдать технологию производства, и использовать качественное сырье. ...
Экономика производства топливных брикетов
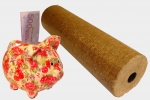
www.ecology-energy.ru
Технология производства топливных брикетов из влажного крупнокускового сырья - - из влажного крупного сырья
Технология производства топливных брикетов из влажного крупнокускового сырья
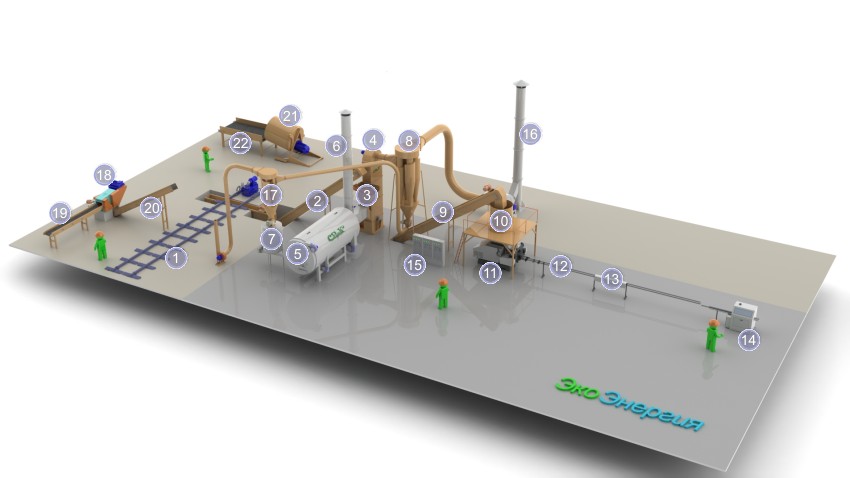
По этой технологии можно производить топливные брикеты из мелких и крупнокусковых древесных отходов (опилки, стружки, щепа, горбыль, отторцовки, шпонрванина, балансы), куриного помета с подстилкой, фрезерного торфа, тростника (камыша), соломы, лигнина, навоза (после ферментации), костры льна и сортированных твердых бытовых отходов (ТБО).
Характеристики сырья: влажность – до 65%, размер частиц – до 6000х250х250 мм.
Бревна, горбыль и т.п. древесные отходы, а также тростник поступают на транспортер (19) и подаются в рубильную машину (18). Из нее щепа или измельченный тростник попадает в транспортер (20) и далее - на механизированный склад “подвижный пол” (1).Мелкофракционное сырьё подвозится автотранспортом (либо погрузчиком) и ссыпается на механизированный склад “подвижный пол” (1).Солома в рулонах поступает на приемный стол (22), затем попадает в измельчитель рулонной соломы (21). Измельченная солома пневмотранспортом направляется на механизированный склад “подвижный пол” (1).
Стокеры подвижного пола имеют гидравлический привод и под его действием совершают возвратно-поступательные движения. Лопатки (“крылья”) стокеров имеют клиновидную форму, поэтому при движении стокеров сырье с регулируемой скоростью подачи направляется к цепному (скребковому) транспортеру (2), далее сырье подается на дисковый сепаратор (3). На нем от сырья отделяется камни, коренья и т.п. примеси, которые попадают в переносной контейнер (на схеме не показан), а сырьё через самотёк попадает в загрузочную секцию Агрегата Сушки-измельчения (4). Сюда же подаются продукты горения из теплогенератора (5) и засасывается холодный атмосферный воздух через аварийно-растопочную трубу (6). Первоначально смешиваются продукты горения и холодный воздух, пропорция смешивания регулируется автоматически, что обеспечивает поддержание заданной температуры теплоносителя. Затем теплоноситель смешивается с влажным сырьем и засасывается в Агрегат Сушки-измельчения (4). В нем сырье измельчается и затем высушивается, поднимаясь в потоке теплоносителя к динамическому классификатору, находящемуся в головной секции Агрегата Сушки-измельчения. Динамический классификатор, частота которого задаётся с пульта управления (15), пропускает мелкое и сухое сырье, а крупные и влажные частицы сырья возвращает к ротору Агрегата, этот процесс повторяется до получения необходимой влажности и степени измельчения сырья. Измельчённое и высушенное сырьё (с этого момента его принято называть мукой) засасывается в осадочный циклон (8) за счет разряжения, создаваемого дымососом (не виден). В циклоне мука осаждается за счет центробежной силы и двигается вниз, а отработанный теплоноситель выбрасывается в дымовую трубу (16). Из циклона мука через шлюзовой затвор подаётся в шнековый или цепной транспортер (9), далее поступает в бункер брикетного пресса (10). Внутри бункера находится устройство, препятствующее слеживанию муки. Из бункера мука шнековым питателем с регулируемой скоростью подачи направляется в брикетный пресс (11). В прессе мука сначала попадает в камеру (или 2 камеры) предварительного прессования, откуда шнеком (или двумя встречно направленными шнеками) подается в камеру прессования. В камере прессования мука вдавливается подвижным поршнем (пистоном) в коническую неподвижную матрицу, где под действием большого давления происходит формирование непрерывного брикета (далее для простоты – «брикетов»). Брикеты, выходящие из пресса, имеют высокую температуру и непрочны, поэтому они направляются в тоннельный охладитель брикетов (12). В процессе охлаждения влажность брикетов уменьшается за счет испарения влаги, и в них происходят физико-химические изменения. В результате они приобретают необходимую твердость, влажность и температуру. Продвигаясь по туннелю охладителя, который в данном случае является одновременно и транспортером, непрерывный брикет проходит металлодетектор (13) и поступает в автоматическую пилу (14), где происходит его нарезка на брикеты заданной длины. Далее брикеты поступают на участок упаковки и склад готовой продукции.
Теплогенератор в данной схеме может загружаться топливом как в ручном (через дверцу), так и в автоматическом режиме - из бункера топлива (7). Пополнение бункера топлива происходит автоматически за счет возврата части муки от осадочного циклона (8) системой пневмотранспорта (17). Опционально бункер топлива может пополняться дополнительным транспортером с отдельного склада топлива (не показан).
Технологии производства топливных шайб и четвертаков имеют незначительные отличия от технологии производства брикетов. Перейти к описанию технологии производства топливных шайб и четвертаков.
Технология производства топливных брикетов в форме параллелепипедов (кирпичиков) имеет незначительные отличия. Перейти к описанию технологии производства топливных брикетов в гидравлических прессах.
Брикеты
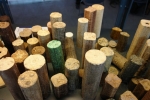
Брикеты - спрессованные частицы растительного происхождения, имеющие форму цилиндров диаметром более 25 мм. (либо имеющие в сечении многоугольник, иногда - с отверстием в центре). Брикеты могут быть изготовлены из древесины, тростника, торфа, куриного помета, лузги, соломы, угольной пыли и многих других видов растительного сырья, а также твёрдых бытовых отходов, макулатуры, использованных автопокрышек. Чтобы получить качественные брикеты, необходимо выполнить 3 основных условия: использовать качественное оборудование, строго соблюдать технологию производства, и использовать качественное сырье. ...
Экономика производства топливных брикетов
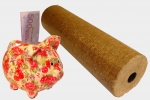
Статья "Экономика производства топливных гранул" дает представление об основных экономических показателях процесса производства топливных пеллет. Аналогично обстоят дела с древесными брикетами, их, наконец-то, распробовали и в России. "Евродрова" охотно покупают и для отопления загородных домов, и для бань, и для каминов. Последнее время спрос на брикеты значительно превышает предложение, из-за чего цена на них иногда доходит до 12 000 руб/т. Такой спрос обеспечивается несколькими серьезными преимуществами брикетов: высокой калорийностью (почти в два раза больше дров) и, самое главное, - длительностью горения - до 12 часов. Экономика производства топливных брикетов по состоянию на апрель 2013 года - в полном тексте статьи.
www.ecology-energy.ru
- Производители сливочное масло
- Выращивание уток на мясо
- Переработка бумаги и картона
- Станок для изготовления пакетов бумажных
- Изготовление брусчатки технология
- Высокорентабельное производство
- Частное производство
- Агентство по организации праздников как открыть
- Сколько можно заработать на рекламе на своем сайте
- Меню пельменной
- Производство полиэтилен
© 2005-2018, Национальный Экспертный Совет по Качеству.